Summary
- Industrial technology aims to enhance the speed and efficiency of the fashion production chain
- Computers, robots, management systems, and cutting machines are just a few examples of it
- Oversee each stage of your production process in a seamlessly integrated manner Try Audaces360 multi-solution for free!
The fashion industry is increasingly embracing industrial technology, especially with the emergence of Industry 4.0 and the development of Industry 5.0 on a global scale.
The COVID-19 pandemic impacted all aspects of human life, shedding light on a reality vastly different from the one we had known.
Consequently, new technological resources gained prominence and rapidly propagated, emphasizing the necessity of adapting to the digital realm.
The industrial sector was among the hardest hit during the crisis.
Sumário
Nevertheless, through investments in technology, the sector has made strides towards recovery and the pursuit of digital transformation, while moving from Industry 4.0 toward Industry 5.0 production.
Continue reading to explore these advancements!
What is industrial technology?
Industrial technology encompasses a set of knowledge, including principles, tools, devices, and more, drawn from various fields and applied to the industrial sector to enhance production speed and efficiency.
These objectives are achieved through the practical application of this expertise, manifesting as a combination of software and hardware working in tandem to optimize processes—an approach commonly referred to as industrial automation.
Examples of applied industrial technology include computers, robots, management systems, and cutting machines, among others.
In the current landscape, technology’s presence is ubiquitous, offering benefits to all segments of the industrial sector that choose to invest in it.
However, a critical consideration lies in the technological maturity of each of these applications.
Over this progress, the industrial sector has traversed several phases, with industrial technology adapting and evolving in its own unique way within each phase.
A brief history of technology in industries
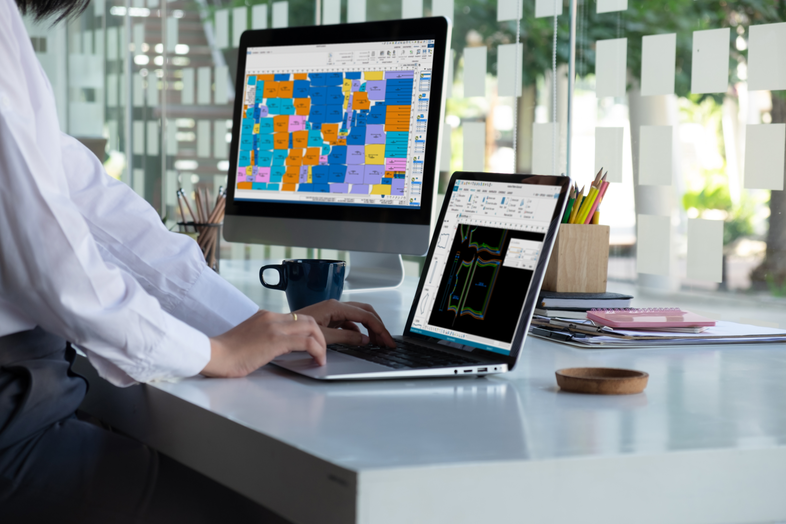
When we envision technology and its role in industry, we often picture large robotic machines, highly sophisticated equipment, sensors, and other devices that are integral to the modern industrial scenario.
But if we delve into the concept of technology, as previously discussed, we find that the roots of industrial technology trace back to the First Industrial Revolution in the 18th century.
Since that pivotal moment, particularly with the advent of the steam engine, the application of knowledge to enhance industrial productivity had already become a tangible reality.
This era is known as Industry 1.0. Subsequently, the journey of industrial development unfolded through two more phases: Industry 2.0, signifying the Second Industrial Revolution of the 19th century, and Industry 3.0, characterized by the introduction of the first computers and electronic devices in the 1970s.
Today, the industry finds itself in a transitional phase as it moves from Industry 4.0 to the emerging frontier of Industry 5.0. While the first brought forth principles of integration, automation, scalability, and real-time responsiveness, Industry 5.0 now seeks to refine these concepts by fostering a new era of human-machine coexistence and cooperation.
Learn more: How does technology in fashion impact the textile industry?
Overview of industrial technology worldwide
Industrial technology has become a driving force in economies across the globe, transforming industries and boosting productivity.
The United States, for example, has been a vanguard in industrial technology, pioneering breakthroughs in automation, robotics, and AI.
Silicon Valley stands as a global hub for tech innovation, embracing cutting-edge technologies in manufacturing and logistics.
India’s growth in industrial technology is bolstered by a strong focus on IT and software development.
The nation’s skilled IT workforce has propelled advancements in software solutions and data analytics, with an increasing emphasis on automation and digitalization for global competitiveness.
England and Italy, with their rich industrial histories, merge traditional craftsmanship with modern industrial tech.
England excels in precision engineering, while Italy thrives in high-end fashion. Both nations blend artistry with technology, demonstrating the potential for industry-specific innovation.
What are the benefits of using industrial technology?
The positive effects of integrating technology into industries are undeniable, driven by its fundamental goal of enhancing operational value and its versatile applications within the industrial landscape.
Below, we outline the primary benefits of industrial technology.
Cost reduction
Producing more with less is a major challenge for companies that want to expand their business.
The application of technology in operations offers a practical and efficient means to achieve this goal.
Automation of tasks eliminates rework, bottlenecks, waste, and other hidden expenses that inflate product costs.
Consequently, production becomes more affordable, facilitating growth and yielding higher profits.
Enhanced productivity
Automated processes inherently outpace their manual counterparts.
Take, for instance, the clothing industry, where traditionally, technical tasks like pattern creation and technical sheet development are performed manually.
However, automation introduces a level of digitalization that brings agility, convenience, and heightened productivity to these processes.
Learn more: How can fashion brands boost their business with technology?
Greater precision and quality in processes
Standardization enables the fine-tuning of processes to maximize precision, ensuring that this heightened level of quality remains consistent throughout production.
The outcome is readily apparent in the form of improved accuracy and superior process quality.
Learn more: What is industrial quality control in the textile business and how does it work?
What is the significance of industrial technology in apparel manufacturing?
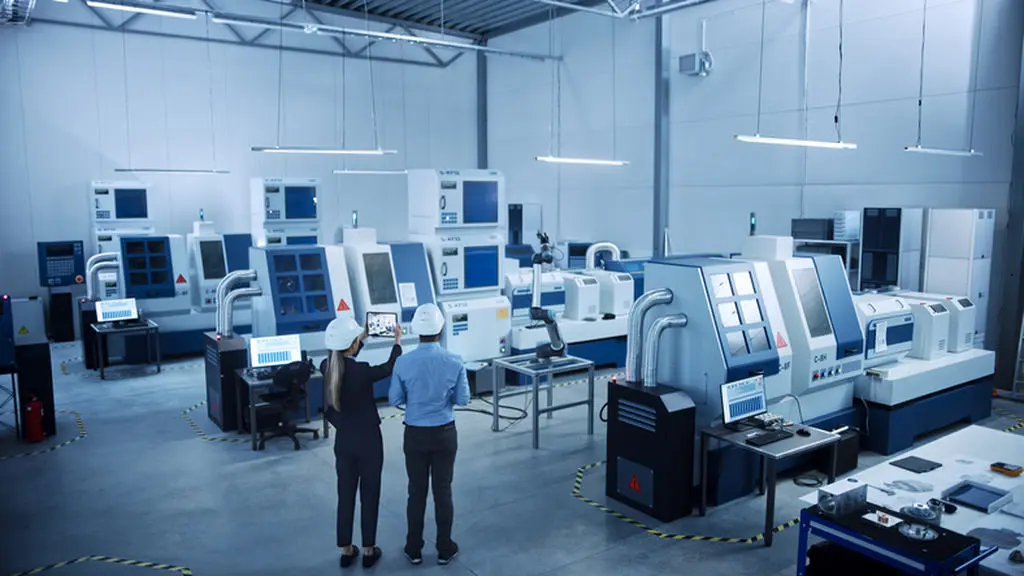
As previously mentioned, the world of fashion demands unique characteristics.
While production in this industry typically follows a linear progression, with each step building upon the previous one, manual processes still play a significant role.
However, we must reconsider the role of technology within this context.
Today, the potential for automation in every facet of clothing manufacturing is a reality – from the creative phase to technical aspects, fabric cutting, and piece assembly.
This transformation is made possible by industrial technology, which, in the context of the Industry 4.0 production model, for instance, offers numerous advantages to clothing companies that invest in automated solutions.
The future is undeniably digital, and apparel companies must adapt to this digital transformation to remain competitive.
Industrial technology: discover key innovations in the market
Having gained insight into industrial technologies and their functionalities, let’s see some illustrative examples and their primary attributes:
Robotization
A direct offspring of Industry 4.0, robotization entails the deployment of advanced or highly intelligent machines within the production line.
These devices possess the capability to execute intricate processes and automate them efficiently.
Artificial intelligence (AI)
Artificial Intelligence (AI) represents the scientific pursuit of creating devices with processing capabilities akin to human intelligence.
This encompasses the capacity to gather, analyze, interpret, and correlate complex information, all while continuously learning from it.
Learn more: All you need to know about sustainable fashion jobs and Industry 5.0
Machine learning
Machine learning is a direct outcome of the application of AI in devices, machines, and robots. For a comprehensive exploration of this topic, we invite you to read our detailed article on the Audaces blog.
Advanced manufacturing
Advanced manufacturing, also known as intelligent manufacturing, comprehends products that undergo cutting-edge industrial processes, often as part of integration within a smart factory.
Cloud computing
Cloud computing involves the storage of vast data volumes in the cloud, facilitating access to information from anywhere and at any time. This database is accessible to both individuals and machines, serving as a foundation for data analysis and interpretation.
Learn more: Learn how to incorporate digital patterns into your production
Internet of Things (IoT)
Also known as IoT, the Internet of Things represents a concept centered on the integration of machines and devices within an extensive interconnected network.
This network enables shared equipment to exchange vital information among themselves, ultimately enhancing production efficiency and technological advancement.
Learn more: What is Web3? Discover all its possibilities for the fashion industry
Experience the apex of industrial technology with Audaces solutions
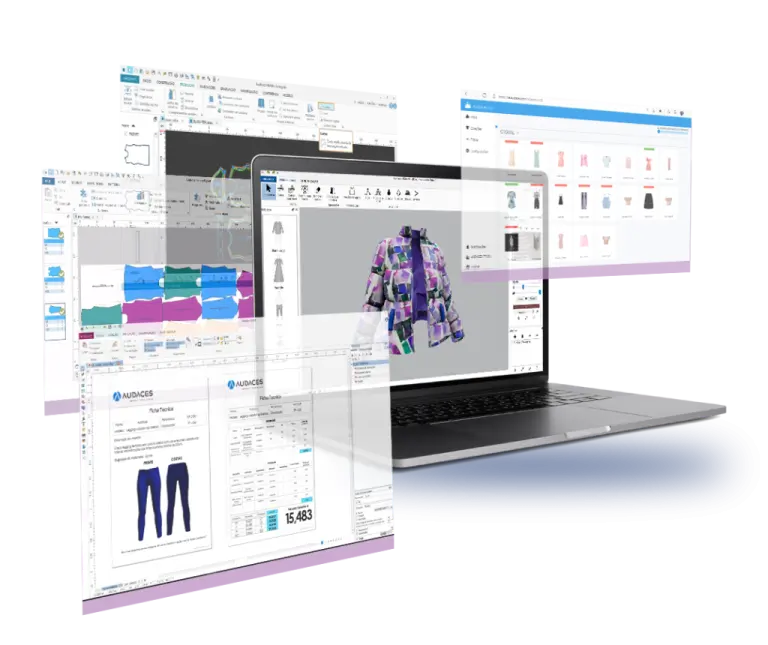
Audaces360 is the ultimate industrial technology solution for the global fashion chain.
It seamlessly integrates cutting-edge technologies like AI, Cloud Computing, and other Industry 4.0 principles, offering a comprehensive suite of software for the holistic management of all clothing processes, from start to finish.
Audaces360
Audaces360 is a comprehensive platform offering a diverse array of tools and resources aimed at various stages of the fashion design and production process.
Its purpose is to streamline workflows, foster collaboration, and boost productivity for fashion designers, pattern makers, and apparel manufacturers.
Below, we highlight some components of Audaces360:
Modeling development
Audaces360 features a robust modeling system that empowers fashion professionals to effortlessly create and modify digital models.
It provides a suite of tools for sketching, grading, and manipulating patterns, along with options to incorporate styling details, seams, and margins.
Snap creation
Within this ecosystem, snap creation software optimizes fabric usage by generating efficient layouts.
It calculates the optimal arrangement of pattern parts on the fabric, minimizing waste while maximizing yield.
Pattern digitizing
Audaces360 supports pattern digitization, enabling users to convert paper patterns into a digital format.
This functionality allows designers to work with existing patterns or digitally enhance them for fine-tuning.
Virtual prototyping
The virtual sample-making feature permits designers to visualize their garments in a three-dimensional environment.
This aids in assessing the fit, flow, and overall appearance of designs before creating physical samples, ultimately reducing costs and time associated with physical prototyping.
Technical files
Audaces360 facilitates the creation of detailed technical packs that encompass design specifications, construction details, measurements, and material requirements for each piece.
These packs serve as vital tools for seamless communication between design teams and manufacturers.
Production planning
The software offers production planning tools to assist in scheduling and managing the production process.
This allows efficient resource allocation, progress tracking, and on-time order delivery.
Collaboration and integration
Audaces360 fosters collaboration and integration among various teams involved in fashion production.
It simplifies the sharing of designs, models, and production data, streamlining communication and workflows.
Cutting Room
Developed by Audaces, the Cutting Room seamlessly manages the precision cutting of parts, harnessing integrated data from intelligent equipment in real-time and offering remote accessibility.
Explore some of the compelling advantages of adopting the Cutting Room:
Quality in pattern cutting
By eliminating the need to redo activities, the Cutting Room facilitates precision and expedites work processes.
When integrated with patternmaking software, it achieves a high degree of automation, bridging the creative and productive phases seamlessly.
Maximized productivity with fewer resources
Minimizing rework processes, the automated Cutting Room significantly enhances productivity.
By eliminating errors and rework issues, your industry can achieve greater output while conserving resources and reducing the time required to attain the same results.
Conclusion
Harnessing technology effectively can set your company apart in the market, giving you a competitive edge. Audaces solutions are designed to empower your company, driving improved results and timely deliveries.
For a deeper understanding on transformative technologies, explore our e-book, which provides comprehensive insights on how to boost your apparel production:
Fill out the form below to download it for free:
FAQ
Industrial technology is the application of knowledge from various fields to enhance industrial operations, making production faster and more efficient.
Industrial technology brings undeniable advantages by adding value to operations and applying resources effectively within an industrial context.
Key innovations in industrial technology include robotization, artificial intelligence, machine learning, advanced manufacturing, cloud computing, and the Internet of Things (IoT).