Summary:
- Industrial quality control is a set of activities that verify whether a product meets the appropriate technical specifications;
- In the textile industry, this practice is essential to identify possible manufacturing defects, avoiding waste and returns;
- Automation brings more agility to quality control after industrialization. Get the free trial of Audaces360!
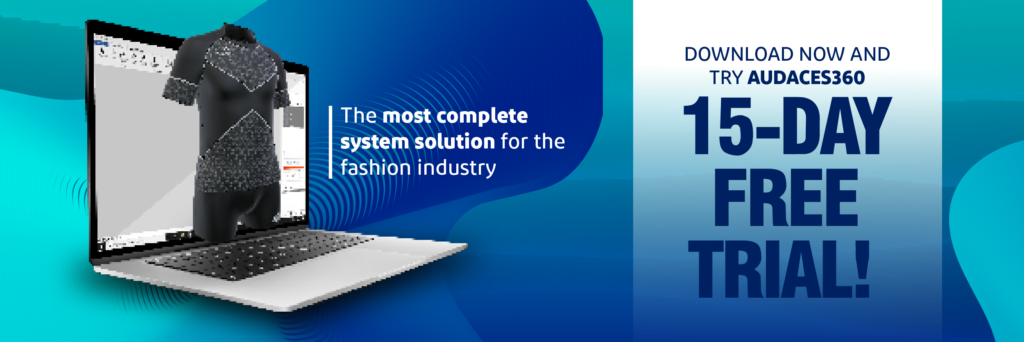
Maintaining standardization is one of the great challenges for any company with large-scale production. And with the fashion industry, it’s no different!
Fortunately, there are strategic measures to address this issue, known as industrial quality control.
As complex as it may be, industrial quality control is an indispensable practice for fashion companies. That is because it ensures that the final product meets minimum quality requirements and considers sustainability, extending the life cycle of clothes and stimulating conscious consumption.
Discover, below, how to ensure the best quality management in your business quickly and effectively.
Sumário
Enjoy your read!
What is industrial quality control?
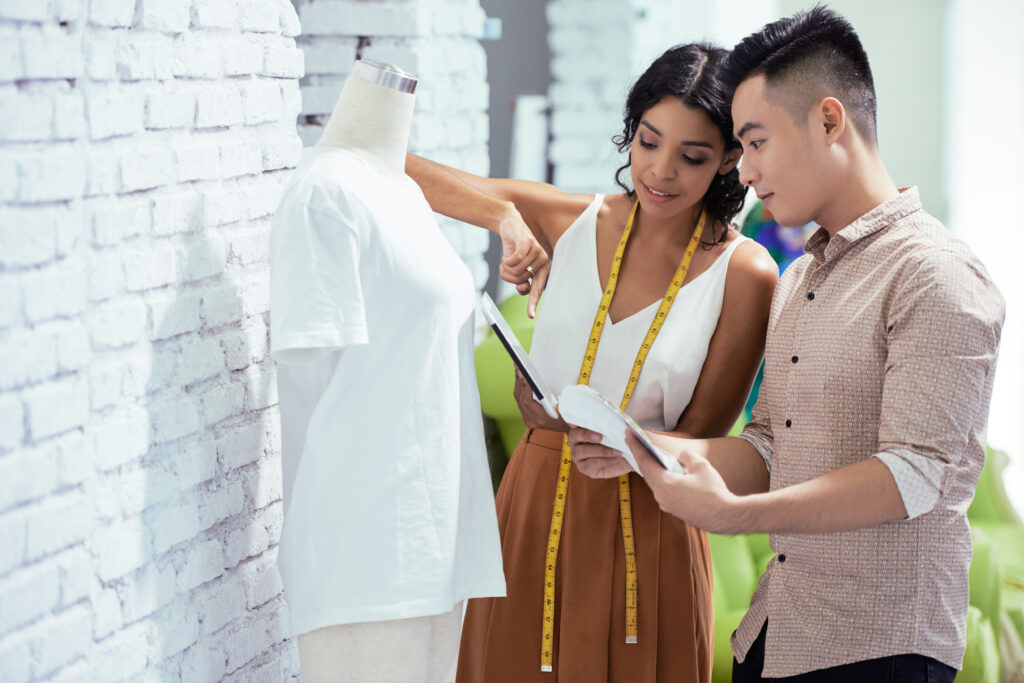
Industrial quality control is the set of activities aimed verifying that the product meets the internal and external quality standards, as well as pinpointing any potential issues, flaws, and discrepancies in the production procedure.
This process is defined and analyzed based on the following steps:
- Design: aspects of style and the aesthetics of the clothing;
- Materials: fibers, threads, fabrics, trims, and other materials used to construct the item
- Production: all processes for fabric construction and garment making, such as spinning, weaving, pattern making, cutting, and sewing.
Learn more: Find out what textile processing is and how it adds value to your production
The importance of industrial quality control
Maintaining standardization is essential because failures jeopardize the efficiency and quality of the product, as well as the visibility and reliability of the brand.
With all these reasons, it’s clear why quality management is so important for the textile industry, right?
Still, we list a few convincing reasons why you should invest in and refine this strategy in your clothing manufacturing. Check them out below:
Keeps consumers safe and satisfied
The final consumers are the ones who will most rigorously evaluate the quality of the product offered by their confection. After all, it is their right to have a satisfactory consumption experience.
In this way, any problem identified has a chance to directly impact the reputation of your business.
This is because, as more interactions take place online and customers share their reviews on social media, they can attract or also discourage new customers from purchasing your product.
So, keep in mind: quality is synonymous with sales, customer satisfaction, revenue, and loyalty for your brand!
In the case of seasonal segments, such as clothing, a fashion collection developed with strict quality control can guarantee consumer interest in upcoming novelties.
Identifies and prevents errors
As we said, one of the functions of industrial quality control after industrialization is to identify errors and bottlenecks in production processes.
This is because, step by step, the final product is evaluated. Thus, if inconsistencies are detected, it is possible to immediately pinpoint the stage that caused them.
In terms of management, this is an excellent resource to prevent future defects and corrections since the practice allows observing patterns and failures in their place and time of occurrence.
Generates guarantee of standardization
Standardization is, at the same time, the main purpose and the great advantage of industrial quality control after industrialization.
In this regard, when well executed, also helps to establish a guarantee of uniformity in the production process, ensuring that all the necessary steps for the desired outcome are taken.
This results in a product that meets the expectations of the customer and is of consistent quality.
Promotes continuous improvements
Finally, one of the benefits of quality control for the garment sector is the constant improvement provided by identifying problems so that they do not recur.
There are also periodic enhancements and eventual changes in quality criteria, as this practice requires reviewing processes from time to time.
What is the purpose of industrial quality control?
As we have already anticipated, the main function of industrial quality control is to improve the standardization of products and processes, making them more agile, efficient, profitable, and sustainable.
Some examples strongly indicate the primordial role of industrial quality control, such as in a clothing company whose pieces are not conforming to the expected patterns of cutting, sewing, and modeling.
This is negative not only in terms of quality but also pricing.
Without adequate control and standardization of the inputs used in production, there can be no uniformity in the final cost, leading to unnecessary wastage and the risk of losses for the manufacturer.
Learn more: How does technology in fashion impact the textile industry?
What are the benefits of industrial quality control?
We can mention several reasons why your clothing company must adhere to industrial quality control.
Discover the primary benefits:
- Continuous quality and improvement of the produced pieces;
- Encouraging a culture of quality and standardization;
- Optimized use and allocation of productive inputs;
- Reduced production errors and rework;
- Minimized invisible costs and maximization of profitability;
- Standardized products and processes;
- Enhanced sales, brand visibility, and customer loyalty;
- Identification of production bottlenecks and anticipation of risks to the production chain.
- Improved production flow: properly manufactured products, no defects, and satisfied customers.
How to do quality control after industrialization?
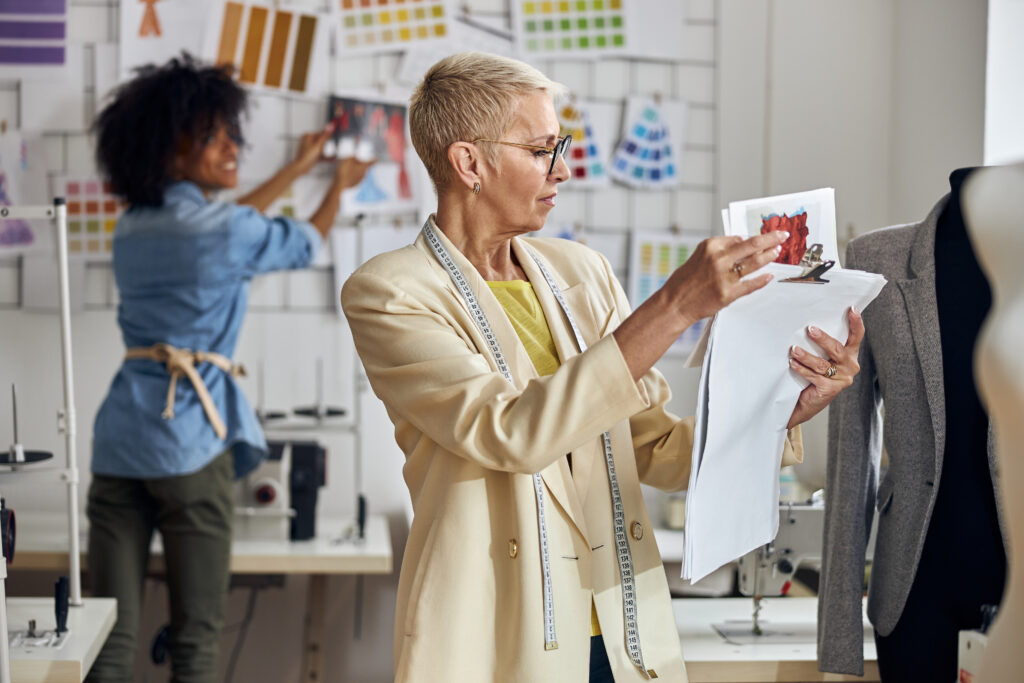
Now that you are aware of the value and advantages of industrial quality control, it’s time to figure out how to apply it to your business.
Here’s a practical guide:
Perform process analysis
The first step in re-evaluating or implementing control management in an organization is to review current processes related to production, management, logistics, and distribution.
It is worth remembering that it is precisely failures of this nature that lead to defects in products.
Define the methods to be used
Errors and production bottlenecks are likely to be identified right from the start. But it’s not yet the time to act on them – first, you must determine the most effective methods to use.
We have already discussed several of them here on the blog: lean manufacturing, just-in-time, PCP, etc. Select the ones that are best suited to your context and get ready to implement them.
Fix bugs
Having raised the problems, the quality criteria, and the best way to solve them, it’s time to get your hands dirty!
Draw up a strategic action plan together with other people responsible for the sectors and start working on remedying the issues in order of priority.
Track customer satisfaction
Ultimately, in addition to maintaining a process monitoring frequency, it is imperative to track the customer satisfaction index. This is the most direct indicator to assess whether the quality of the product is meeting expectations.
Learn more: Why consider sustainable consumption and production for your company?
What are the main quality control tools?
Keeping track of so many productive steps is not the easiest of tasks. Therefore, relying on the help of some specific tools makes all the difference.
Discover the main recommendations:
Pareto Diagram
The Pareto Diagram, or Pareto Chart, is an especially important tool for quality management because it allows you to organize the causes of a problem in an orderly way.
It is also possible to prioritize demands according to the severity of the problem.
PDCA cycle
Another troubleshooting tool is the PDCA cycle (plan, do, check, act). Through the actions prescribed in the methodology, it is possible to get an interactive and efficient action plan.
Checklists
Checklists are often data collection and analysis worksheets. In the context of quality control, they serve as an active control tool, organizing and facilitating the resolution of tasks.
How is textile quality control management in practice?
As we have already seen, quality control is responsible for ensuring uniformity in production, using established technical specifications as a guide.
The last sewn piece should be the same as the first. Even though a pattern maker may be able to create one perfect garment, it is much more difficult to maintain quality in the mass production of thousands of pieces.
Get to know other specificities of the quality control applied to the garment segment:
Random or individual sampling
To ensure that production is conducted accurately and effectively to prevent returns, garments that are in the manufacturing process and those that have been completed must be inspected one by one – or by random selection.
Technical specifications
Quality control professionals not only check the seams but also compare the measurements to the original technical specifications.
On-site inspection
Quality Assurance teams sometimes may need to travel to check the quality at faction factories. If errors are found on the first inspection, the production manager attempts to correct them at the cutting or sewing stages.
How can technology help industrial quality control?
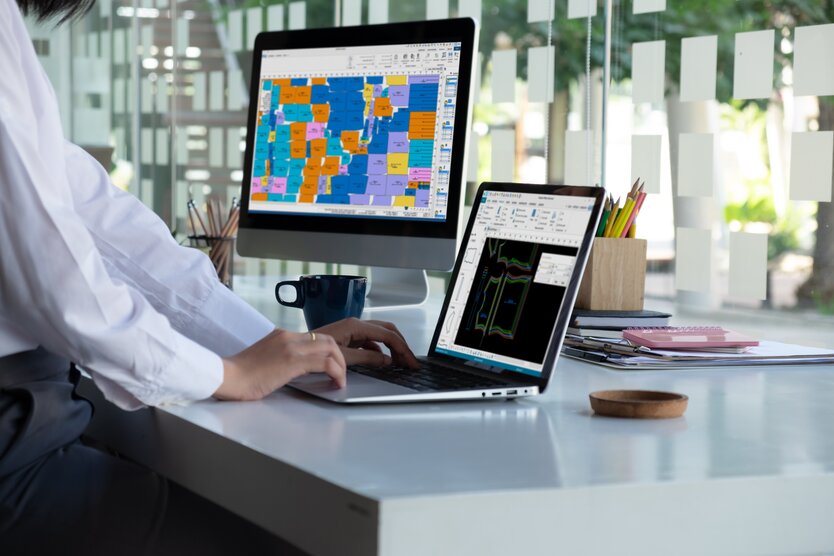
Industrial quality control is a complex universe that encompasses a broad selection of variables, such as types of fabrics, designs, printing, and maintaining a solid bond with dependable suppliers to deliver the pieces to the final consumer.
Given the level of detail in management, added to the new requirements of Industry 4.0, technology becomes fundamental for successful industrial quality control.
Moreover, investing in automated management helps your fashion business in executing more sustainable production practices. In this regard, explore what Audaces can offer:
Audaces360
Audaces360 is a comprehensive and innovative multi-solution that integrates all processes, from creation to production.
This system can be a powerful asset in the production process for adapting the products to the due technical criteria, reducing waste, remanufacturing, and returns.
Audaces Isa
With Audaces Isa, you can control and organize all the technical aspects of your fashion collection!
Fashion PLM Audaces Isa was designed to help manage the lifecycle of fashion products, something essential for anyone wanting to launch a clothing line consciously and assertively.
Audaces Marker
Having good management of resources is a mandatory step for your clothing business to reach the desired profitability. Audaces Marker helps you in this economy, allowing the maximum use of fabric.
Audaces’ automated marking system provides rapid laying of any part in just a few minutes.
Conclusion
Now that you know how to apply the most effective industrial quality control system for your company, find out how Audaces helps you get ahead of the competition.
Grab our complimentary e-book for free now:
FAQ
Industrial quality control is a set of actions and procedures designed to ensure that a product properly meets technical specifications.
The first step is to evaluate all processes and select the most suitable tools. Then, the pieces must be inspected and compared to the original measurements. Often, it may be also necessary to visit the factory in person.
Because the practice is responsible for standardizing products and processes, making them more efficient, profitable, and sustainable.