Summary:
- There are various textile printing techniques, each one offering unique benefits for your work
- Dive deeper into the characteristics, advantages, and available types of these printing methods to determine the best fit for your needs
- Elevate your fashion collection creation with Audaces360 multi-solution. Don’t miss the chance to access the free trial now!
Prints are a captivating aspect of the fashion industry, influencing clothing choices in line with trends and seasons.
Timeless patterns such as animal prints, polka dots, and florals continue to enchant customers, designers, and fashion entrepreneurs globally, maintaining their enduring stylishness.
The art of textile printing, whether carried out through digital or manual processes, boasts a rich history spanning centuries. This history has allowed for the transfer of designs onto a wide array of fabric types.
Among the diverse array of printing methods, silk-screen printing stands out as the most popular option, while sublimation printing offers a cost-effective solution. Digital printing, on the other hand, is emerging as a cutting-edge and eco-friendly choice.
Sumário
So, get ready! Today we will share a comprehensive guide to the top 6 textile printing techniques and their practical applications, which will assist you in selecting the perfect fit for your business.
Enjoy your reading!
What is textile printing?
Textile printing is the process responsible for transferring designers’ creations onto the chosen material. It’s a highly delicate and detail-oriented method that adds a unique touch to each piece.
The individuals involved in this process include the surface designer, responsible for creating the print designs, and the textile printer, who ensures that the designer’s designs are accurately reproduced on the fabric.
Whether aspiring to be a surface designer or a textile printer, dedication to learning and delivering quality work is essential.
For instance, the textile printer takes on the responsibility of the actual printing. They prepare inks and materials, adjust machinery, and organize the workspace. In addition to the printer, there is also the printing assistant who manufactures and finishes the pieces.
To become a skilled textile printer, a comprehensive understanding of each step in the process is crucial. To further develop your skills, you can consider taking courses such as:
- Textile printing
- Printing
- Textile design
- Fashion
- Fashion design
- Textile illustration
Besides, each technique yields a different type of material. There is a wide array of print designs and various methods for their production. Explore these further below:
6 primary textile printing techniques
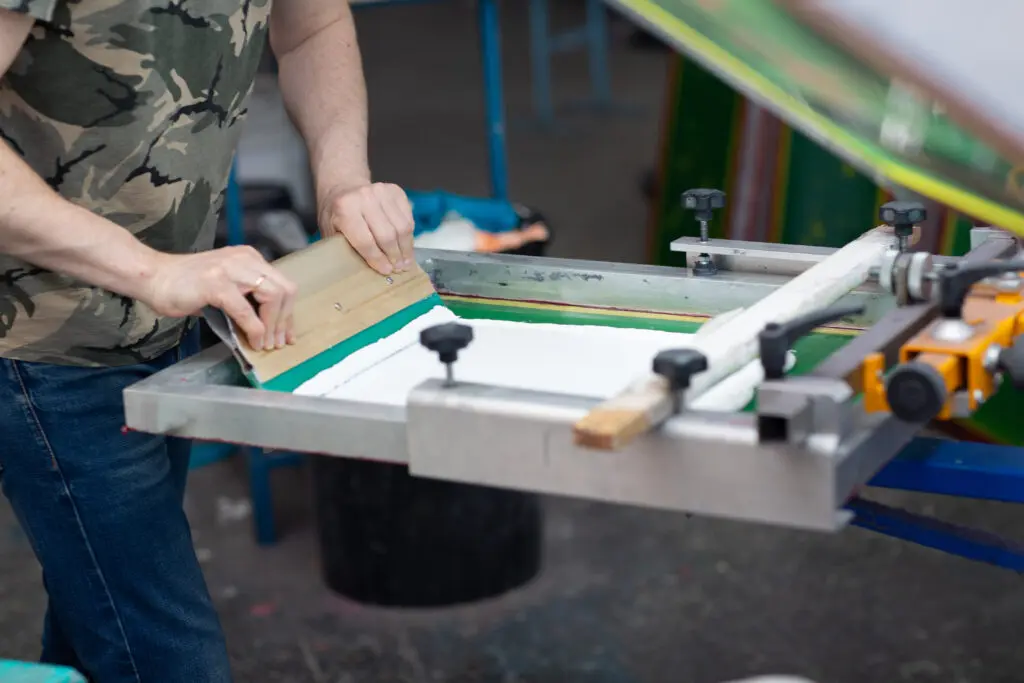
Printing encompasses a variety of methods, each offering unique advantages to your work. Some of these techniques have been in use for centuries, while others have developed as a result of post-Industrial Revolution advancements.
To decide the most suitable textile printing technique, it is crucial to discover which one offers greater profitability and alignment with the core objectives of your business.
To provide you with a comprehensive understanding of how each printing method functions and its practical applications, we’ve assembled a guide on the subject:
1. Heat transfer
Heat transfer printing involves transferring an image onto a clothing item using a heated thermal board.
The process begins with the application of ink from the transfer onto the t-shirt. Subsequently, pressure is applied for a few seconds at the appropriate temperature, causing the image on the transfer to fuse with the fabric.
This method is known for its sophistication and the ability to achieve a wide range of colors and shapes. The durability and final quality of the garment depend on the type of mesh or fabric used.
2. Sublimation printing
Sublimation printing is a cost-effective and highly favored technique in the printing industry.
It relies on a chemical process that transforms the print from a solid state to a gaseous state without passing through a liquid phase.
As a result, the ink, which is initially in solid form on paper, transitions to a vapor and adheres to the fabric.
Although it might sound complex, sublimation printing only requires sublimated paper with a design, a heat press, and a smooth surface to work effectively.
It’s worth noting that this textile printing process is efficient and suitable for large-scale production.
However, it is primarily recommended for fabrics with a higher percentage of polyester and lighter colors. Sublimation is not suitable for printing on dark fabrics.
3. Silkscreen
One of the most renowned and ancient techniques, silkscreen printing involves the application of paint through stencils supported by a porous fabric mesh.
Although this textile printing is typically a manual process, modern technology has introduced machines that can assist in this method. During the process, ink is forced through a polyester or nylon screen by pressure and then pulled across the screen using a squeegee.
In this meticulous process, each color must be printed in the exact location and in a specific order. The screens used in silkscreen printing display both dark and light dots.
The dark dots represent the areas where ink is pushed through the screen, while the light dots indicate areas that are impermeable to ink, preventing the passage of light. Additionally, the process necessitates the use of planks to stretch the fabric.
Silkscreen printing, also known as serigraphy, has the capability to reproduce even photographs on fabric. The color system employed in this technique is CMYK.
Bring your silkscreen designs to life before printing! Our free e-book shows how 3D design can help you create realistic simulations ahead of production. Download now!
4. Laser printing
Laser printing is a modern process that offers high-quality prints, but it has some limitations.
Not all fabrics can be used because the laser can burn certain materials. This method involves a printer that uses standard toner and transfer paper.
5. Digital printing
Technological, high-cost, and innovative, digital textile printing is one of the most modern techniques in printing.
This method is produced using specific technology, which makes it more expensive and restricts its use to certain fabrics due to ink fixation issues.
Its production involves printing the design directly onto the fabric’s surface.
This is advantageous as it offers intricate detailing, precision, and the ability to experiment with colors, all while maintaining prints faithful to the expected outcome.
Learn more: Discover the best types of fabric for sublimation printing
6. Rotary printing
Rotary printing covers the entire fabric and features sequences of image patterns.
It involves metal cylinders with perforations through which ink passes onto the fabric, where it is fixed.
This method is generally limited to a maximum of three colors, as the more colors used, the higher the printing cost.
While the initial cost of rotary printing may be higher, it becomes more cost-effective with a larger volume of prints produced.
How to choose the ideal textile printing method for your design?
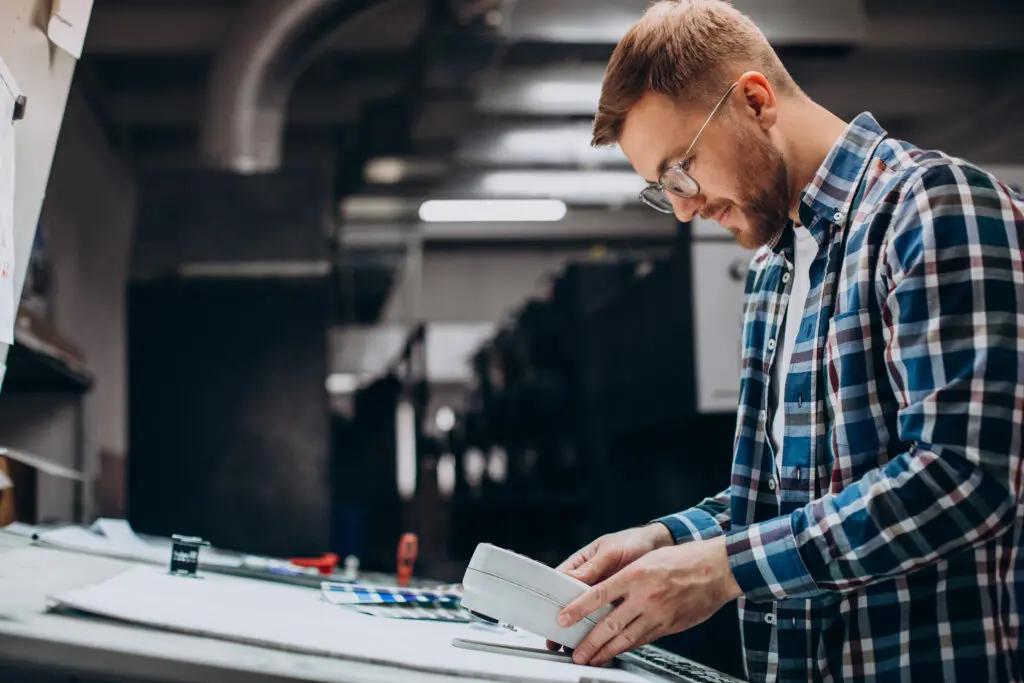
Now that we’ve explored the top 6 textile printing techniques, you might be pondering how to match the right method with specific types of designs and determine which printing solution best suits your business. Worry not; the answers are just around the corner!
Localized prints
This is the most traditional method employed in the textile industry, involving individual pieces. It’s typically carried out through traditional screen printing.
Printing is limited to specific areas of the fabric, such as the chest, back, sleeves, and so on.
Localized prints can be created using various techniques, including screen printing and sublimation. This approach utilizes a silkscreen matrix that is applied directly to the fabric, enabling one-at-a-time printing.
In addition to clothing, this technique is applicable to a range of products, including personalized items like pens.
Continuous or all-over prints
In contrast to localized printing, continuous printing covers the entire fabric. It can be executed in various ways, including frame-by-frame continuous printing, faux continuous printing, cylinder-based continuous printing, and digital continuous printing.
Here’s a closer look at each of these methods:
Rotary screen printing
In this textile printing technique, the process is carried out on a fabric roll. The rotary screen print utilizes serigraphic screens with engraved frames.
With the engraved frame, silkscreen prints are applied to the entire fabric roll.
The rotary silk screen printing process involves color separation to engrave and apply colors individually. However, it’s important to pay attention to the seams, as they can disrupt the continuity of the image.
Learn more: When to use rotary printing? Get to know the advantages of this technique
Roller printing or cylinder printing
The roller printing process is similar to rotary screen printing, but instead of frames, metallic cylinders are employed to transfer ink onto the fabric.
Seamless print
When using this textile printing method, it is essential to work with fabric pieces that have already been cut and do not have seams, or to print on the entire fabric without interruptions.
All-over digital printing
In this case, the most suitable technique is digital printing, which allows direct printing of the desired image from a computer.
The results of digital printing are excellent, and it accommodates images ranging from small to large scales.
Which textile printing method has the longest lifespan?
Now that we’ve explored various types of textile printing and prints, you might still have some lingering questions, such as which one offers the greatest durability.
In addition to the care provided by the piece’s owner, sublimation is the most recommended technique for achieving optimal longevity. But what’s the reason behind this recommendation? Sublimation prints are resistant to peeling, cracking, or scratching, making maintenance easier for the end consumer.
It’s worth noting that digital printing, harnessing the power of technology, can also ensure print standardization—a feature not always achievable with traditional techniques.
How to choose the right fabric prints?
When it comes to printing on clothing, several factors need to be considered, including the fabric type, intended use, and production quantity.
For instance, garments crafted from polyester and dry-fit materials are well-suited for sublimation techniques. If you plan to print on cotton fabrics, it is advisable to explore other methods, such as screen textile printing and digital printing.
Learn more: 9 fabrics with the perfect fit to use in your fashion collection
How to select the ideal print type for your collection?
It’s essential to bear in mind that, much like the meticulous process of creating a garment where the best raw materials are carefully selected, choosing the right textile printing technique follows the same principle.
To ensure that the chosen method yields outstanding results and delivers an aesthetically pleasing product to the end customer, it’s crucial for the person in charge to understand that the best print type is one characterized by quality and seamless integration with the chosen fabric.
Explore the digital textile printing tool in the Audaces Pattern system
When it comes to enhancing and streamlining your textile printing process, you can rely on Audaces Pattern to deliver the solution!
The digital printing process is entirely computerized, eliminating the need for frames or cylinders. It operates exclusively through a textile program linked to an industrial printer.
Audaces Pattern is a component of the comprehensive Audaces360 multi-solution system, fully equipped to work with digital printing. It simplifies the entire pattern development process, whether it involves placement or rotary prints.
This technology is fast, efficient, and cost-effective. It enables you to manage prints and patterns, increasing agility and optimizing time in the process.
Conclusion
As demonstrated, the entire textile printing chain involves skilled professionals, specialized knowledge, and cutting-edge technology, all of which can lead to superior outcomes for your collection.
Your choice may depend on whether you prioritize higher quality or lower costs, among other factors. With a variety of printing types and techniques available, the next step is selecting the one that best aligns with your goals and preparing for success in this ever-expanding market.
Want to learn more? Discover Audaces360 and explore our comprehensive suite of solutions for the fashion industry.
FAQ
Textile printing is the process of transferring a designer’s creation onto a chosen material, involving intricate work that imparts uniqueness to each piece.
The main printing techniques include Transfer, Sublimation, Screen Printing, Laser, Digital Printing, and Rotary Printing.
Digital printing, aided by technology, ensures consistent print standardization.