Summary
- Natural fibers account for 40% of global textile fiber usage
- The interplay of effects, fibers, and colors gives rise to a multitude of thread types, introducing innovative textures to fabrics
- Gain confidence in classifying, treating, and utilizing textile fibers. Experience the benefits of Audaces360 multi-solution with our free trial!
Take a moment to conduct an experiment: how many different types of fabrics can you identify around you?
Go beyond just considering the clothing you’re wearing; observe the upholstery on your chair or sofa, the curtains, or even the seating in your car.
At the heart of all fabrics lie textile fibers. These fibers form the basis of yarns, which are then woven into fabrics. These fabrics serve myriad purposes, ranging from furnishing to creating entire clothing collections!
Now, let’s dive into this subject! How many varieties exist? How can they be categorized? What sets them apart in terms of characteristics?
Sumário
If you’re curious about uncovering these answers and exploring the realm of fibers, yarns, and fabrics, join us in the comprehensive guide below.
Happy reading!
Classification of fibers based on origin
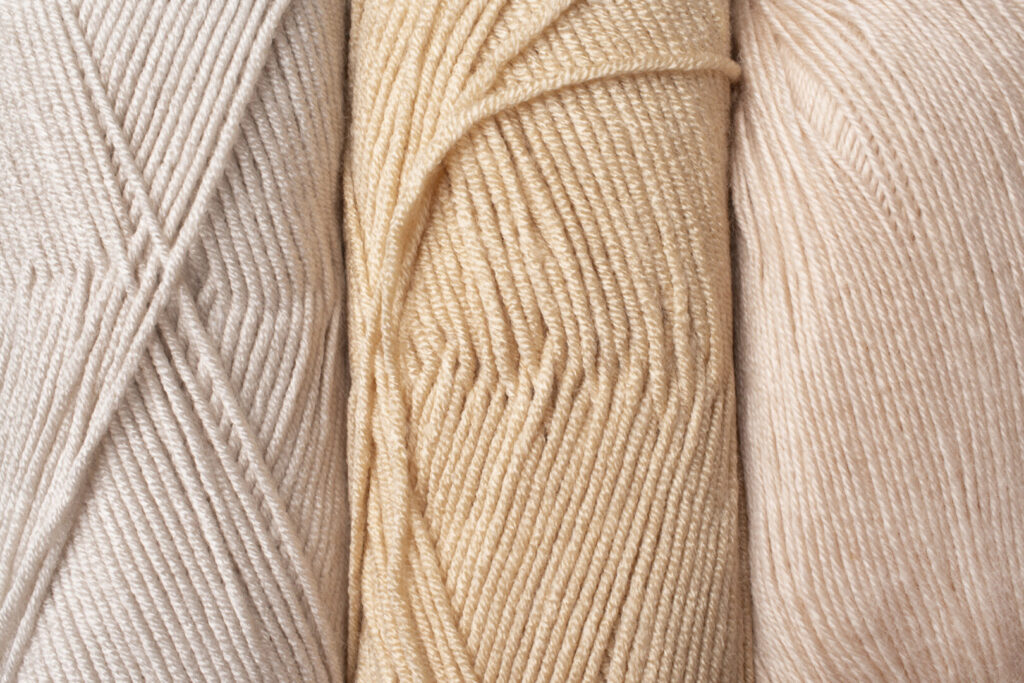
When considering their origin, textile fibers can be categorized into three main types: natural, artificial, or synthetic.
Textile fibers of natural origin
Constituting 40% of the world’s textile fibers, natural fibers emerge as filaments within the framework of nature. Their classification draws from their source—plants and animals. This dichotomy leads to their subdivision into two primary categories:
Fibers derived from animals
This category encompasses fibers extracted from animal hair bulbs and those procured from the secretions of lepidopterans or mites, as exemplified by the silkworm.
The former includes noteworthy fibers such as sheep, alpaca, vicuña, cashmere, and camel wool. These species epitomize the essence of this type of fiber.
The latter species yields silk and byssus. Of these, silk holds prominence.
It emerges from the glandular secretions of the silkworm during its larval stage, before embarking on its transformation into a chrysalis and eventually, a butterfly.
Regions such as China, Japan, India, and Italy stand as bastions of superior silk production, both in terms of diffusion and quality.
Both silk and wool exhibit distinct characteristics. They effortlessly embrace dyes, adeptly absorb perspiration, and modestly conduct heat.
When it comes to maintenance, a gentle touch is essential. Washing them at lower temperatures with neutral or slightly alkaline detergents ensures their longevity and vibrancy.
Fibers of vegetable origin
Fibers derived from plants’ cellulose represent a rich tapestry of possibilities.
These fibers hail from various plant components: seeds yield fibers like cotton and kapok, stems contribute to flax, hemp, jute, and ramie, leaf veins provide raffia and sisal, and even fruits yield fibers like coconut.
Among these, cotton stands as the foremost contender—a product of the delicate down-enveloping seeds within the Malvaceae family.
Inherent in plant fibers are thermal recovery, thermal conductivity, and an affinity for dyes. While they excel at absorbing perspiration, their prowess falls slightly short of wool’s capabilities.
Learn more: 9 fabrics with the perfect fit to use in your fashion collection
Artificial textile fibers
Artificial fibers, originating from natural counterparts, undergo meticulous human intervention through chemical processes.
These interventions are necessitated by the irregular surface or inadequate length of natural polymers for transformation into extended strands.
Taking center stage is rayon—a collective term encompassing all yarns produced from derivatives of cellulose. Depending on the specific chemical procedures employed, an array of yarn types emerges (including viscose, cupro, acetate, and more).
The artificial nature of these fibers bestows several advantages: the attainment of desired fineness and length, controlled luminosity and opacity, the flexibility of dyeing during processing, and heightened efficiency due to the absence of impurities.
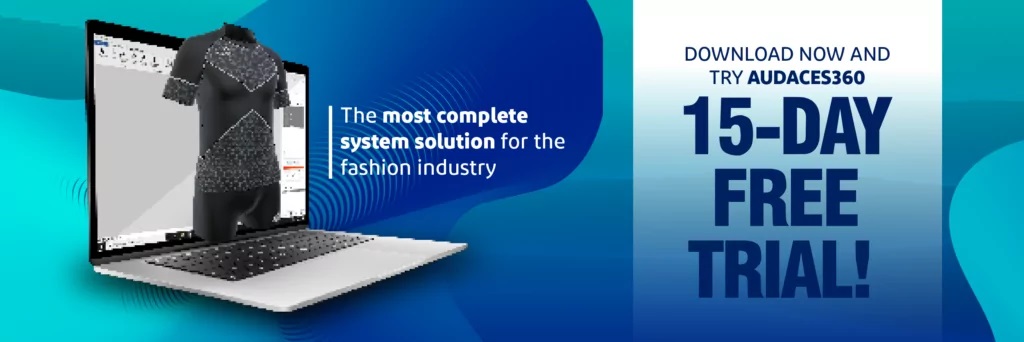
Synthetic textile fibers
The realm of synthetic fibers (“man-made” fibers) unfurls through synthesis processes, utilizing raw materials rarely found in the natural domain.
Comprising 55% of fibers employed in clothing and furniture production, synthetic fibers fall into distinct “families” based on their constituent polymers.
Among the stalwarts of this category reside nylon, polyester, and acrylic fibers.
Characteristic hallmarks of synthetic fibers include their feather-light nature, enabling heightened fabric yield.
These fibers boast thermoplasticity, resistance to water infiltration, effortless laundering, and commendable durability.
In contrast, they bear certain drawbacks, including diminished thermal stability, feeble moisture absorption, restricted breathability, and susceptibility to static electricity.
Furthermore, their hydrophobic properties render them resistant to conventional dyeing techniques, necessitating the use of specialized dyes.
When it comes to textile fibers, synthetics often encompass short-staple elements, eschewing spinning in favor of cohesive adhesion.
This fusion results in layered textures of specific thickness and fabric consistency, as exemplified by materials like felt.
The interplay of fibers and yarns in textiles
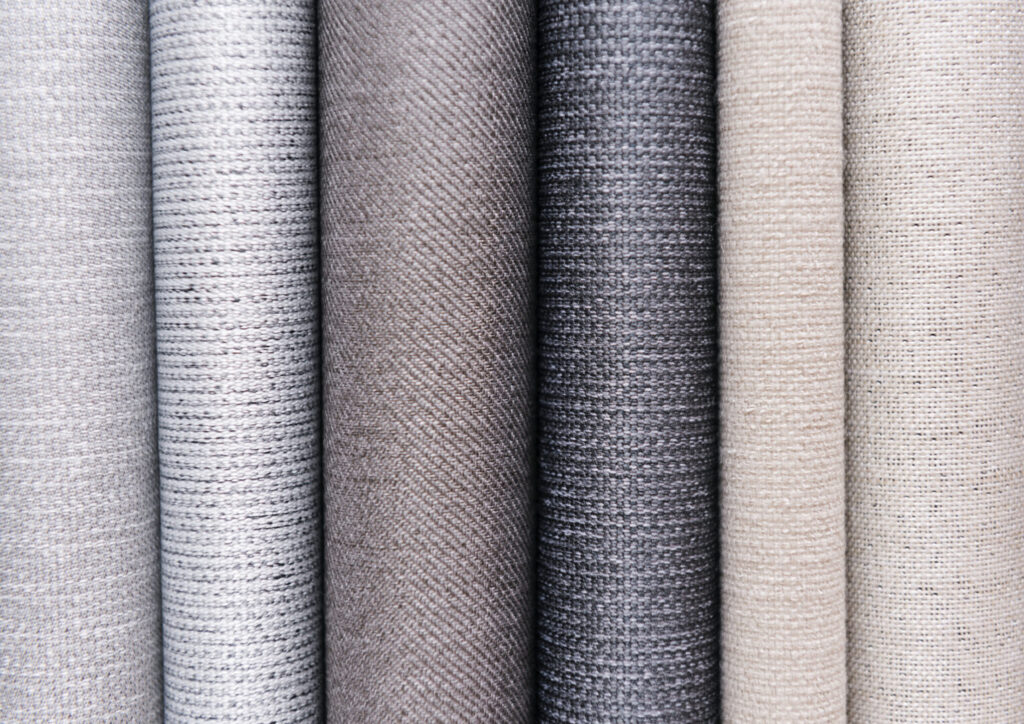
Within the realm of textiles, the connection between fiber-spinning processes gives rise to threads. These threads, in sequence, culminate in the creation of fabric.
The process isn’t solely mechanistic; it’s a canvas for creativity. By artfully blending effects, fibers, and hues, a plethora of thread varieties emerge, each one with its unique textures.
The possibilities amplify further, contingent upon the amalgamation of fibers, their lengths, twists, and thicknesses.
It is within this combination that the textile domain unveils a spectrum of quality and price differentials, presenting a dynamic landscape of choices.
Learn more: Uncover the fabric composition chart and the most utilized types
Why is it important to know textile fibers?
Understanding textile fibers extends beyond comprehending the mere yarn fabrication process; a deep dive into the very fibers that constitute it’s imperative.
Delving into the origin, traits, and recommended applications of textile fibers holds paramount importance. Their influence directly shapes the quality of the final product.
Whether hailing from the realm of natural, artificial, or synthetic origins, each fiber category boasts distinct attributes that merit careful consideration.
This acquires even greater significance within the apparel industry, fashion shows, and global fashion events.
Think high breathability for summer wear, thermal insulation for battling the cold, or even hypoallergenic properties for garments in direct contact with the skin.
This understanding of textile fibers underscores their pivotal role in steering the trajectory of the final creation.
Learn more: Learn all about satin fabric and how it can elevate your fashion production
How are fabrics and textiles structured?
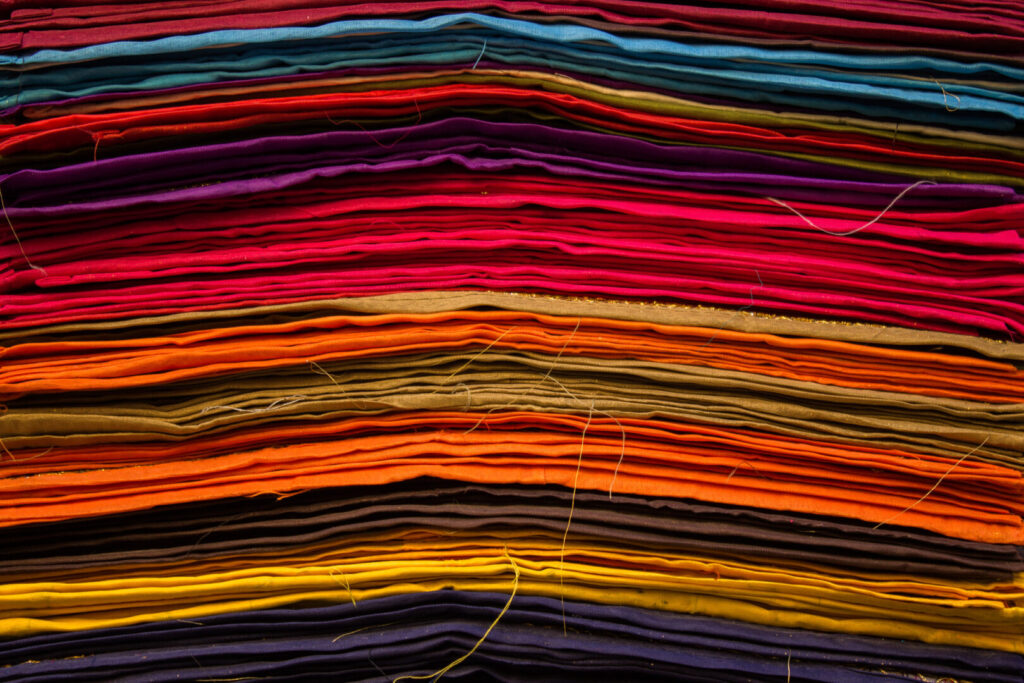
Ever wondered how fabrics come to life? They emerge as versatile, pliable sheets, shaped by the harmonious or random intertwining of the very yarns and fibers that constitute them.
This weaving process necessitates a dimensional framework, achieved through a series of carefully orchestrated processes and ingenious combinations.
The interplay of weft and warp intersections, or even the fusion of materials through melting and chemical transformations, gives birth to an array of fabric types.
Each fabric not only takes on distinct visual patterns but also embraces specific physical attributes—flexibility, foldability, stretchability, elasticity, and more—integrated into the very fabric of the material itself.
A classification system for fabrics is rooted in their structural composition. This is determined by the manner in which threads interact, leading to several fundamental fabric structures:
- Interlaced threads: The threads weave in and out, creating complex patterns
- Adhesive or fusion action: Threads fuse together, generating unique textures
- Resultant from fiber solutions: Threads converge from solutions, forming distinctive fabrics
- Special mixed solutions: A blend of methods results in distinctive hybrid fabrics
To grasp the complexity of textiles, one must explore the materials involved.
It is possible by navigating through numerous genetic classifications of synthetic fibers, excluding natural ones, culminating in a staggering minimum of 25 fundamental fabric structures and their assorted variations.
Distinguishing the face and reverse of fabrics
Ever pondered over the significance of identifying the right side of a fabric? This seemingly minute detail holds the power to transform garment creation, sparing us from mishaps and wastage.
In some instances, discerning the front and back of a fabric is straightforward—especially evident in prints. Other times, it requires a dash of intuition.
To aid in this pursuit, consider the following criteria that lend clarity to distinguishing the reverse side:
- Fabric: Typically, the fabric’s reverse side rests on the exterior of the roll
- Lustrous: Silky textiles tend to boast enhanced shine on their right side
- Selvedge: If the fabric producer’s name is printed on the selvedge, that’s the right side; when it’s embroidered or woven, that’s the correct face
- Tactile: A smoother texture often signifies the right side, while coarser textures hint at the reverse
- Weaving: The warp is usually more pronounced on the wrong side
- Lace: Embossed patterns on lace serve as indicators of the right side
Given its role within the industry, a comprehensive understanding of fabric attributes, classifications, and fit properties is imperative for all professionals involved in clothing production.
This knowledge underpins meticulous planning and ensures garments are created with precision and suitability in mind.
Learn more: Learn more about crepe fabric and its various uses in fashion
Categorizing fabric quality
In today’s market, a diverse array of fabrics with varying technical specifications graces our choices. Yet, when it comes to utilizing these textiles in production, do you understand the criteria governing their quality classification?
Different industries and applications may have specific criteria for evaluating fabric quality, but there are some common parameters that are often used:
Fiber content and composition
The type of fibers used in a fabric can greatly influence its quality.
Natural fibers like cotton, wool, silk, and linen, as well as synthetic fibers like polyester, nylon, and rayon, all have different characteristics that contribute to the overall quality of the fabric.
Thread count
Thread count refers to the number of threads per square inch of fabric.
Generally, a higher thread count indicates a finer and smoother fabric, often associated with better quality.
Weave or knit structure
The way threads are woven or knitted together affects the fabric’s appearance, texture, durability, and performance.
Different weaves and knits have varying properties, such as breathability, flexibility, and strength.
Tensile strength and durability
The ability of a fabric to withstand tension and stress without tearing or breaking is an important factor, especially in applications like apparel and upholstery.
Finishing treatments
Additional treatments such as anti-wrinkle, water-repellent, stain-resistant, or flame-retardant finishes can influence the fabric’s quality and suitability for specific purposes.
Certifications and standards
Various international standards and certifications, such as OEKO-TEX, GOTS (Global Organic Textile Standard), and ISO, provide guidelines and requirements for fabric quality and sustainability.
Defect scoring
Central to fabric quality classification is the defect “score”. This score serves as the cornerstone for determining fabric quality levels.
This classification covers fabrics that contain defects such as:
- Continuous defects exceeding 3 meters, attributable to spinning, weaving, dyeing, or finishing—excepting stains
- Fabrics bearing stains combined with other aforementioned defects shall receive a Second Quality classification
- Discrepancy in hue between the fabric’s center and edge (center-edge), as well as between the commencement and conclusion of the pieces (end to end)
- Width diverging from product specifications
- Non-standard color may diverge from the nuances stipulated for First Quality
- Stretch potential surpassing the specifications designated for the article
Learn more: Find out how to use linen fabric in your fashion collection
Fabric enhancement: 10 key treatment methods
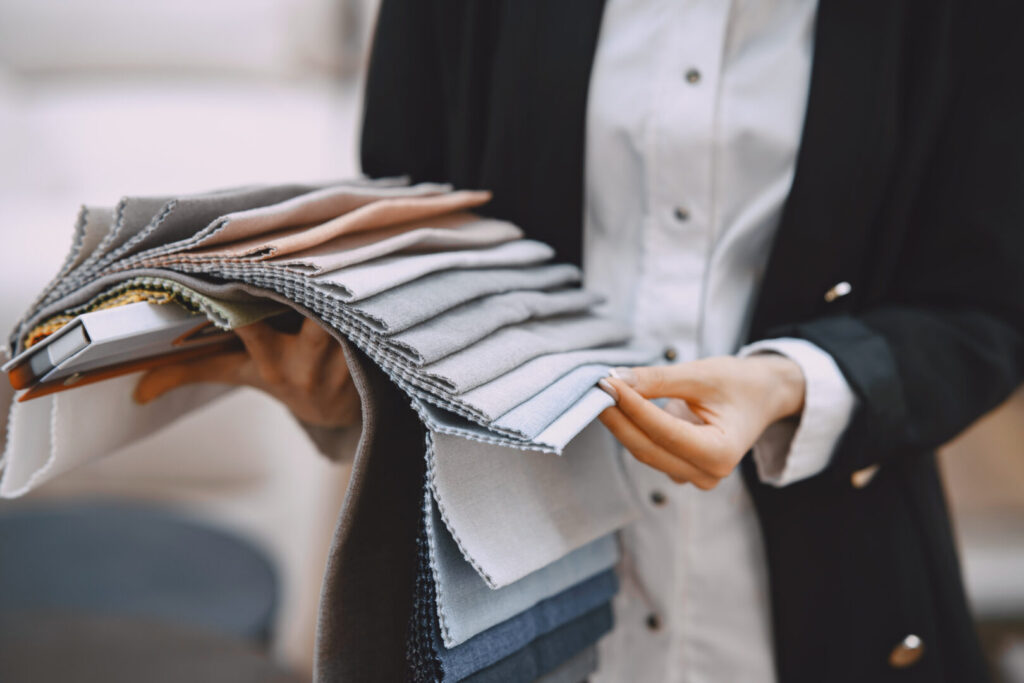
Upon completion of the weaving process, fabrics can undergo various textile treatments.
Each of these finishing techniques serves the purpose of altering the fabric’s appearance and/or structural characteristics.
These treatments aim to enhance attributes such as flexibility, hardness, and the removal of residual impurities present in the fibers.
Explore the following compilation of primary treatment methods that can be employed to tailor fabrics for both industrial and apparel applications:
1. Bleaching
Bleaching involves the application of bleaching agents, such as hydrogen peroxide, sodium hypochlorite, or sodium chlorite, to lighten the fabric’s fibers.
This treatment is typically employed with natural fibers that possess a yellowish hue. Its primary purpose is to prepare the fabric for subsequent processes, such as optical bleaching, dyeing, or printing.
Following the bleaching stage, it is essential for the fibers to undergo a thorough wash to eliminate any residual chemical substances from the material.
2. Optical whitening
Even after undergoing the bleaching process, certain fabrics may still exhibit a faint yellowish tint.
In such cases, the optical whitening procedure is applied.
This enhancement technique involves the utilization of a (usually heated) product that reflects bluish and violet wavelengths, counteracting the presence of yellow tones.
The outcome is a fabric that appears even whiter in color.
3. Stentering
Stentering is a process wherein fabrics are secured solely by their selvages and are passed through an oven for drying and/or thermosetting.
Notably, the fabric surfaces do not come into contact with any other surfaces during this operation.
This treatment is commonly employed on synthetic fibers and serves multiple objectives.
It helps fix the fabric’s width and weight while also stabilizing the threads, contributing to enhanced dimensional stability and overall fabric quality.
4. Sanforization
Sanforization is a process aimed at inducing mechanical shrinkage in the fabric along the warp direction (length).
During the fabric’s manufacturing, threads are often stretched and put under tension. Without undergoing a fiber relaxation process, they are prone to shrinking after washing.
Sanforization is primarily employed for cotton fabrics to counteract this tendency.
5. Calendering
Calendering involves subjecting the fabric to high pressure and temperature as it passes between cylinders in a specialized machine.
Through this method, the fabric’s surface is compressed, resulting in increased reflectivity of light.
This imparts a heightened shine and a superior tactile quality to the fabric’s surface.
Learn more: Explore what muslin fabric is and its creative possibilities for collections
6. Gas singeing
The gas singeing process is designed to eliminate protruding fibers from the fabric by subjecting them to controlled burning. This action ensures a uniform surface across the fabric.
Small, disorderly filaments are often removed using hot plates or flames.
This procedure is crucial for maintaining the integrity and consistency of prints, preventing potential issues with irregularities or lack of durability.
7. Desizing
Desizing is a technique employed to eliminate sizing agents that are introduced into the fibers during the initial stages of fabric production.
These agents form a protective layer on the fabric, potentially hindering the effectiveness of subsequent processes.
The removal of these substances is crucial to ensure optimal application of further treatments.
8. Scouring
Scouring is a wet cleaning process conducted in an alkaline environment.
Its primary objective is to remove impurities present in the fibers, including fats, resins, paraffins, oils, and other contaminants.
9. Napping
In the napping process, fine filaments are raised on the fabric’s surface, resulting in a fluffy and textured appearance.
Other names for napping are gigging, genapping, teaseling, and raising.
10. Sanding
Sanding involves creating a fibrous surface on the fabric.
This method produces a “peach skin” effect on the fabric, though the raised fibers are typically smaller than those achieved through the napping process.
Sanding is accomplished using cylinders covered with sandpaper, and their motion contributes to the desired surface texture.
Learn more: What textile processing is and how it adds value to your production
Discover the ideal fabric for your collection with Audaces
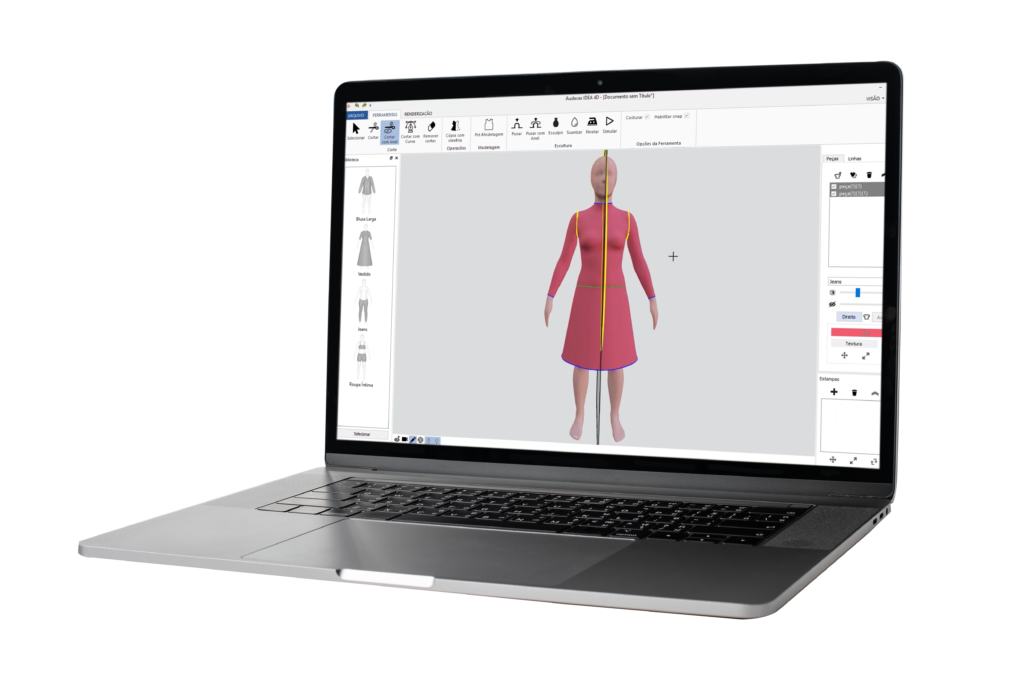
These processes undoubtedly unveil the intricacies inherent in the classification, treatment, and eventual utilization of textile fibers.
But what about embarking on the journey of digital transformation and its pervasive influence on industries worldwide?
Let’s explore some Audaces solutions, which empower you to harness the potential of textile fibers and amplify their value within your apparel production.
Audaces Fashion Studio
Audaces Fashion Studio is a software program that streamlines visual communication among teams and expedites the commercial approval of designs.
It encompasses the present and future solutions for the fashion industry.
With Fashion Studio, you can enjoy a multitude of benefits, including:
- Virtual and digital fabric trim simulation
- Application of realistic colors, prints, and textures
- Reduction in the number of samples required during the creation phase
- Clear and efficient communication between the styling and patternmaking teams
- Cost reduction in the creation phase, enabling precise adjustments
- Clear and lifelike visualization of designs on the computer screen
- And much more!
Audaces Idea
Professionals seeking an agile solution for their work can turn to Audaces Idea!
This platform offers tools for technical drawing, tecg packs, and automatic pre-costing to facilitate improved communication and ensure accurate production.
Audaces 3D
The perfect partner to help you overcome the challenges of collection development, eliminating tight deadlines, creation problems, and rework: meet Audaces 3D!
This software allows you to:
- Approve drawings and modeling
- Verify fit and wearability of garments
- Approve the initial sample digitally
- Reduce the need for physical sample garments
- Save time and expenses with prototyping
- Create more sustainable processes
- Generate images for Marketing and Sales teams
- Enable a realistic online fitting room
Interested in gaining a comprehensive understanding of fabric types from A to Z?
Download our free e-book now to find out more about textile fibers, fabric quality, fabric draping, and the finest choices to elevate your clothing production to new heights!
FAQ
Textile fibers are essential elements used in fabric production, encompassing natural (cotton, wool) and synthetic (polyester, nylon) materials that are woven or spun together to create diverse fabrics.
Understanding fibers is vital for selecting fabrics that suit specific needs, considering attributes like strength, comfort, and sustainability, thus enabling informed choices in fashion and industry.
Fabrics form through weaving (interlacing warp and weft), knitting (looping yarns), or nonwoven methods (bonding fibers), yielding a wide array of textiles tailored for distinct applications.