Summary
- The way a factory is organized affects efficiency, costs, and even worker safety.
- That’s why choosing the right layout is key to a smooth textile production process.
- Experience the future of fashion with Audaces360. Start your free trial now!
While it might look like a simple architectural element, factory layout is the foundation of a productive company.
Each type has its own benefits. Some work best for large-scale production, while others fit smaller, flexible operations. Identifying the best option will help businesses improve their workflow.
We’re here to assist! If you’re establishing a new factory or optimizing an existing one, you’ll find all the necessary information. From clear explanations to practical tips, our insights can guide your decision.
Happy reading!
Sumário
What is a factory layout?
A factory layout is how machines, equipment, and workstations are arranged in a production space. It defines how materials and workers move through the factory.
Each factory has different needs. The layout must fit the type of products you work with. It should also consider space, workflow, and safety.
An organized layout reduces wasted time and effort, helping workers complete tasks faster. Moreover, it improves communication between different sections.
It’s important to keep in mind that planning a factory layout requires careful thinking. Factors like production volume, storage, and worker movement matter.
Ultimately, this leads to a layout design that fosters productivity, communication, and improved space efficiency. It establishes a structured setting for seamless operations.
What is the purpose of a factory layout?
The main purpose of a factory layout is to improve efficiency. It organizes machines, materials, and professionals in the best way. This reduces delays and increases production speed.
A good layout also helps with safety. It prevents overcrowding and reduces the risk of accidents. Workers have clear paths to move and perform their tasks.
Space management is another key goal. The right layout makes full use of available space. It avoids clutter and makes storage easier.
Finally, a well-planned layout supports flexibility. If production needs to change, you can provide adjustments quickly.
Learn more: Boost your garment manufacturing with industrial management
Main types of factory layouts
Factories use different layouts, each serving a specific purpose. The best choice depends on the type of production.
Here are the main types:
Cellular layout
A cellular layout groups machines and workers by process. Each group, or cell, focuses on a specific task.
This setup is especially common in small-batch production, as the goal is to reduce movement and waiting time. Workers stay close to their tasks, making production faster and improving problem-solving.
Cellular layouts are perfect for customized products. They allow quick adjustments when changes are necessary. This makes them ideal for flexible manufacturing.
Learn more: Top 5 technologies driving mass customization in clothing
Functional layout
A functional layout places similar machines together. For example, all cutting machines are in one area, and all assembly stations are in another. This is useful when producing different types of products.
It helps factories handle various tasks without major changes. Workers move materials between sections as needed. While this increases flexibility, it can also slow down production.
This layout is best for factories with varied products. It allows specialized workers to focus on specific tasks. However, careful planning is key to avoid delays.
Linear layout
A linear layout follows a straight-line process. Materials move from one station to the next in a fixed sequence. This setup is common in mass production.
It reduces handling time and keeps workflow steady. Since tasks follow a set order, production becomes faster and more predictable.
Linear layouts work well in industries like automotive and electronics. They help factories produce large quantities quickly and efficiently.
Learn more: How can mass production boost your apparel manufacturing?
Fixed-position layout
A fixed-position layout is used when the product is too large to move. Instead of moving the product, workers and machines come to it. This layout is common in shipbuilding and construction.
It allows for complex assembly processes. Large projects require many specialized tasks, and this layout supports that.
However, space management is a challenge. Factories using this layout must plan it carefully to avoid congestion.
Why implement a good factory layout?
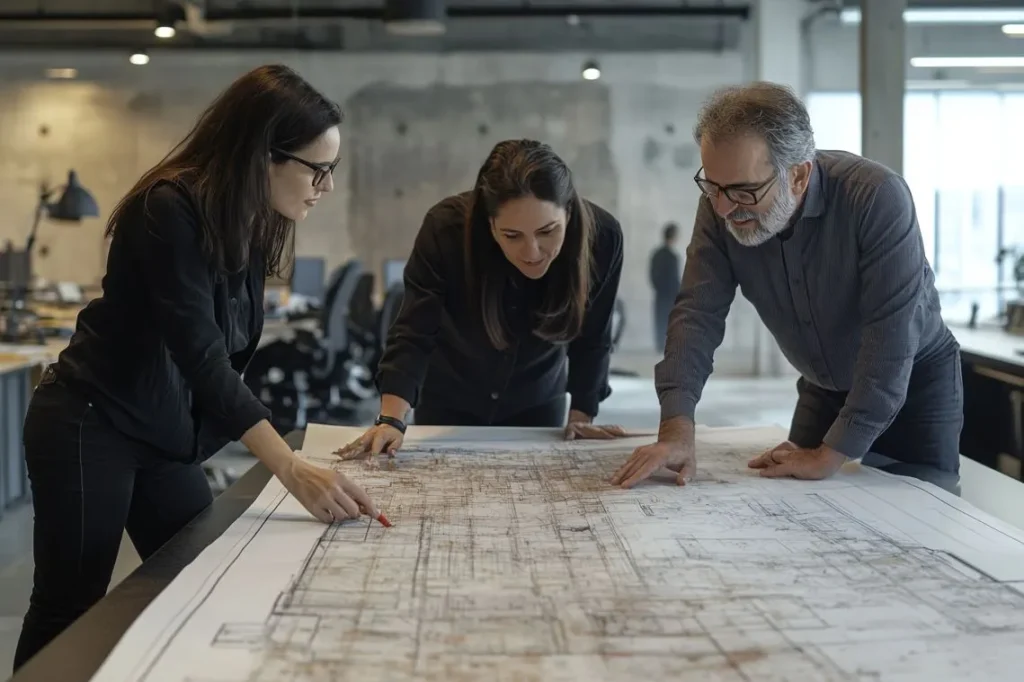
A thoughtfully designed layout boosts efficiency and organization. It creates a seamless workflow and optimizes production.
These reasons will convince you of the importance of investing in your fabric layout:
Maximum productivity
A good factory layout increases productivity. Workers complete tasks faster when everything is in the right place. Machines operate smoothly, reducing downtime.
Shorter travel distances save time. When materials move efficiently, production runs without delays. Workflows become more predictable and controlled.
Clear paths prevent congestion. If workers and machines don’t interfere with each other, operations stay consistent. This also reduces errors and rework.
Productivity improves when factories reduce waste. A well-structured layout minimizes movement, waiting, and unnecessary handling. This leads to faster and more cost-effective production.
Efficiency in movement and flexibility
An effective layout should reduce unnecessary movement. Workers and materials reach their destinations faster, reducing delays and improving efficiency.
Flexibility allows factories to adapt to new demands. When production needs changes, a smart layout is easier to adjust. You can rearrange machines and workstations quickly.
When workers don’t have to walk long distances, they save time and can focus their full attention on their tasks.
Learn more: 5 strategies to optimize your production with efficient fashion
Better use of space
An effective layout makes the best use of available space. It prevents overcrowding and ensures an organized factory.
Storage areas should be easily accessible, so a good layout must place materials in the right spots. They need to be within easy reach of their respective areas.
This all contributes to enhancing workflow. That should be the constant focus. Correct circulation between spaces guarantees the easiest and quickest execution of tasks.
Integration between workstations
Workstations should connect smoothly. When teams and machines work together, production runs faster. The role of factory layout planning is to improve communication.
Proper integration reduces delays. Workers pass materials efficiently from one station to the next. This keeps the process flowing.
A connected workspace also boosts teamwork. When workers see how each step fits together, they collaborate better. This leads to a stronger and more productive operation.
Discover the ultimate fully integrated cutting room! Schedule a free consultation and get a custom project designed just for you.
What to consider when designing your factory layout?
A factory layout must support smooth workflow and efficiency. Key factors include space, movement, and production needs. Check out the following:
People flow
The movement of personnel within a factory directly impacts efficiency and safety. A well-designed layout prioritizes clear pathways, minimizing unnecessary travel and potential bottlenecks.
This not only saves time but also reduces the risk of accidents and collisions, creating a safer work environment.
Production volume and variety
The volume of production directly influences the layout’s design. High-volume production lines often work better with linear layouts.
In these layouts, machines are placed in a row to improve the flow of materials. This setup minimizes movement and maximizes output.
Conversely, a factory producing a variety of products may require a more flexible layout. Functional layouts, which group similar machines together, allow for adaptability and efficient handling of diverse product lines.
Learn more: How to define production stages using a textile flowchart
Material storage
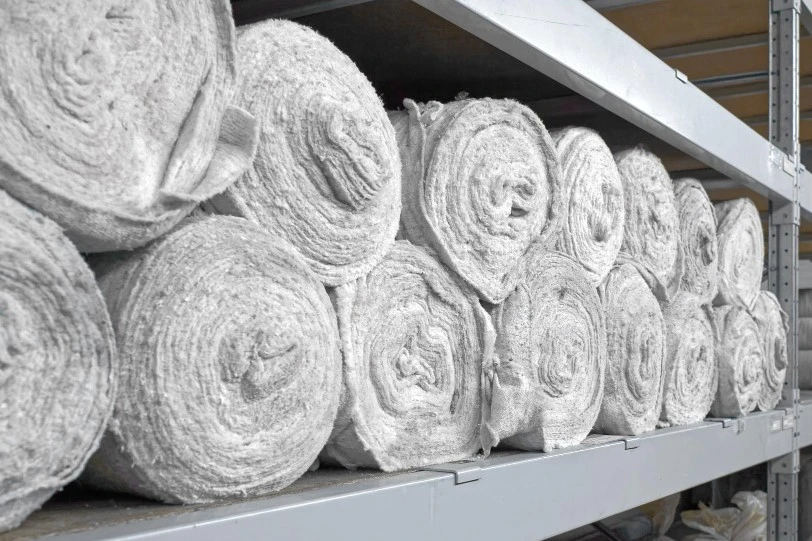
Efficient material storage is vital for minimizing downtime and maximizing production flow.
Storage areas should be strategic, ensure easy access and minimize transportation distances. This reduces handling time and prevents delays in the production process.
The type of materials also dictates storage requirements. Heavy or bulky materials may require specialized storage solutions and handling equipment.
Distance between machines
The distance between machines directly affects workflow efficiency and worker safety.
Optimizing machine placement minimizes material handling and worker movement, reducing cycle times and improving overall productivity.
Adequate spacing between machines also ensures worker safety and comfort. Sufficient space allows for safe operation and maintenance, reducing the risk of accidents and injuries.
Overhead material handling
Overhead material handling systems, such as cranes and conveyors, can significantly improve efficiency in large-scale production environments.
These systems allow for the safe and efficient movement of heavy or bulky materials. This frees up floor space and reduces manual labor.
Integrating overhead handling systems into the factory layout requires careful planning and coordination.
The layout must accommodate the system’s infrastructure, including support structures and pathways.
Main problems of a poorly designed factory layout
- Increased material handling: Longer distances between workstations lead to excessive movement of materials, increasing labor costs and time.
- Reduced productivity: Poor workflow design disrupts production flow, causing delays and lowering output.
- Increased safety risks: Narrow pathways and cluttered areas increase the risk of accidents and injuries.
- Higher operational costs: Inefficient material handling and workflow lead to increased labor and energy costs.
- Communication breakdown: Poorly placed workstations and departments hinder effective communication and collaboration.
- Quality control issues: Inefficient material flow can damage the product.
Learn more: How can technology enhance the quality of textile products?
How to create a factory layout?
- Analyze production requirements: Determine production volume, product variety, and material flow.
- Map material and product flow: Trace the movement of materials and products through the factory.
- Determine space requirements: Calculate the space needed for workstations, storage areas, and material handling.
- Develop layout options: Create multiple layout designs based on production requirements and space constraints.
- Implement and monitor: Implement the chosen layout and monitor its performance.
How technology helps in factory layout planning?
Technology plays a crucial role in modern factory layout planning. It enables businesses to optimize their production processes and improve efficiency.
Specifically, machinery designed for seamless integration significantly optimizes space and production.
Integrated systems reduce the need for excessive buffer areas and material handling. Machines communicate with each other to synchronize operations. This allows for a more compact and efficient layout, freeing up valuable floor space.
Furthermore, the ability to monitor and control the entire production line from a centralized system enables real-time optimization. The result is increased productivity and reduced waste.
Optimize your factory layout with Audaces Cutting Room
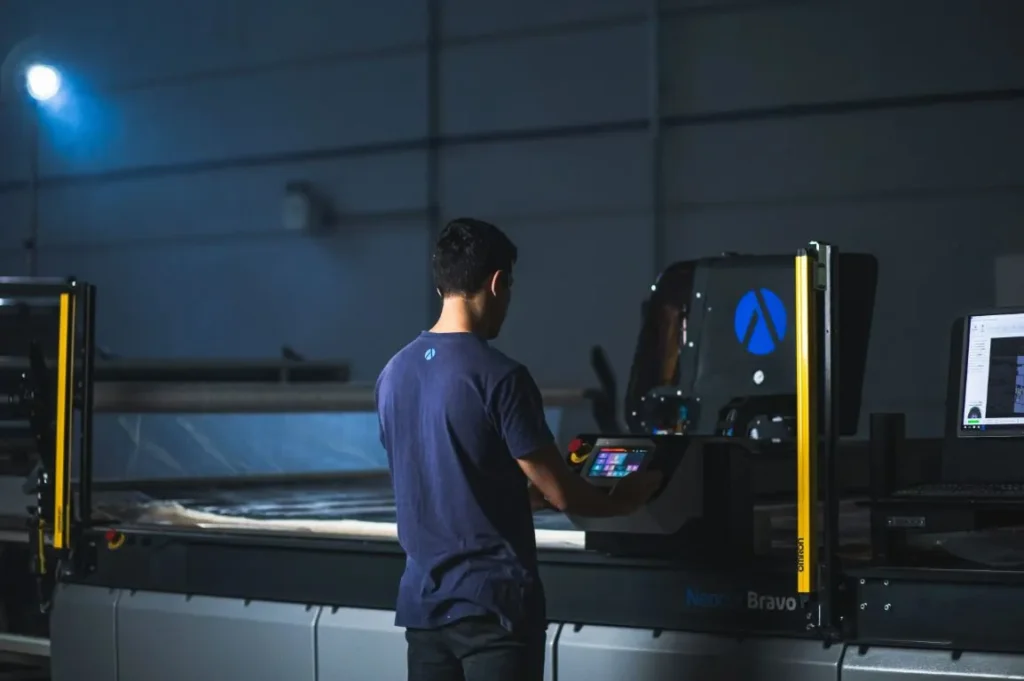
Audaces brings you cutting-edge technology designed to transform your textile manufacturing!
Our Audaces Cutting Room equipment prioritizes precision, delivering zero-gap cutting and exceptional accuracy across a wide range of fabrics.
We understand that reliability is paramount. This is why we build our machines with high-quality components for maximum durability and minimal maintenance.
Beyond our hardware, Audaces Cutting Room is powered by intelligent software to streamline your workflow.
Audaces ICF is our system that empowers production managers by seamlessly receiving complete production requests and automating the creation of efficient cutting order schedules.
Did you find this article helpful? Let us know what you think in the comments!
FAQ
A factory layout is how machines, equipment, and workstations are arranged in a production space. It defines how materials and workers move through the factory.
The main purpose of a factory layout is to improve efficiency. It organizes machines, materials, and professionals in the best way. This reduces delays and increases production speed.
The most popular types of factory layouts are cellular, functional, linear, and fixed-position.