Summary
- High-quality fabric creation is an essential step in the entire apparel industry. For this reason, it is key to know each step of how it is made.
- Making your own fabric with partners instead of buying pre-made can save money for your business.
- Technology is essential to achieve excellent results, as in all areas of fashion. To optimize your company today, try Audaces360 for free!
Fabric creation happens since the world is world. Back in the Neolithic Period, around 6000 BC, people used primitive techniques to make coverings and insulation.
Since then, fabric creation has evolved with new techniques and purposes. Optimized processes and technological materials enable innovative designs in a short period.
Our goal with this guide is to provide you with a comprehensive understanding of the entire process. This way, you can explore the possibilities that fabric creation can bring to your business.
Enjoy your reading!
Sumário
What is the importance of fabric creation for the fashion industry?
Fabric creation serves as the base upon which fashion designers build their creations. The properties and textures of fabrics define design choices, influencing fit, draping, and overall style.
Choosing carefully is important because it affects the aesthetic appeal of fashion items. Unique or high-quality fabrics can elevate the perceived value of garments and enhance brand perception.
Delving into the realm of costs, the fabric creation process significantly impacts the final price of a garment. Smaller companies have less power to negotiate because they buy ready-made fabrics or smaller amounts of fabric.
In such situations, raw material ends up becoming more expensive. When it comes to large productions, it is possible to reduce this cost.
Buying yarn in bulk lowers prices and gives you the opportunity to negotiate with suppliers for weaving and dyeing.
Learn more: 9 fabrics with the perfect fit to use in your fashion collection
How is fabric created?
As you might imagine, fabric creation involves numerous steps. Different suppliers carry out each of these stages, requiring several skills and machinery.
The most basic step to start understanding this process is to know about fiber selection. They can be either natural or synthetic. Then, machines twist these fibers into yarns before making them into mainly woven or knitted fabrics.
Nowadays, when we talk about natural fibers, we can also talk about food-related fabrics. Including fibers obtained from mushrooms, coffee, milk, potatoes, and various fruits. Yes, that’s right. This is how much technology has evolved!
Learn more: Learn methods for printing on fabric to make impactful collections
What are the main stages of fabric creation?
Now, let’s delve into step by step how the production of most fabrics works.
Fiber selection
This is the initial stage of fabric creation. The choice of fibers significantly impacts the properties and characteristics of the final fabric.
As mentioned, we can classify fibers into two main categories:
- Natural fibers: derived from plants (cotton, linen), animals (wool, cashmere, silk), or biological materials (mushroom leather and bamboo modal).
- Synthetic fibers: these are fibers created from chemicals (nylon, polyester, and acrylic), or biological materials combined with synthetics (milk cotton and coffee leather).
Learn more: Uncover the fabric composition chart and the most utilized types
Spinning
The fibers undergo a meticulous process involving several steps to transform into yarn at this stage.
First, the fibers are cleaned to remove impurities and sorted based on length, color, and quality. Next, the fibers are carded, a process that aligns and disentangles them to create a fluffy web.
This web is then drawn out to make it thinner and stronger. Then, the fibers are further stretched and twisted together during drafting, forming a continuous strand known as yarn.
The thickness and twist of this yarn determine its properties, such as strength, drape, and texture. This combination of qualities results in a wide range of options to choose based on the desired outcome.
Weaving and knitting
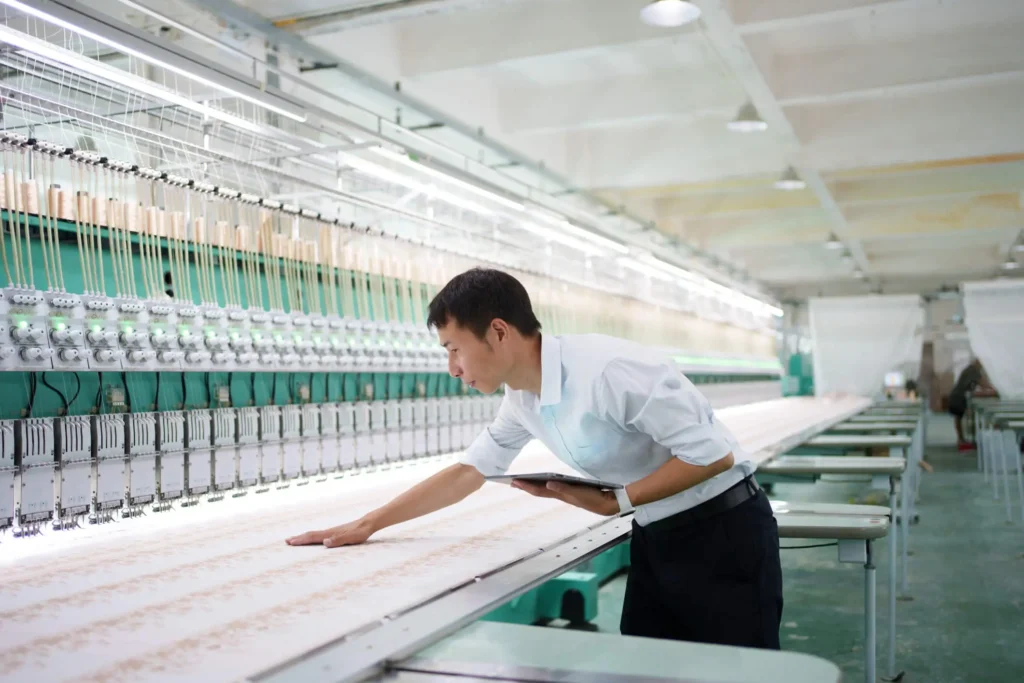
These are the two primary methods of fabric creation.
Weaving involves interlacing two sets of yarn — the warp, which runs lengthwise, and the weft, which runs crosswise — to create a flat fabric.
Various weaving techniques yield diverse patterns and textures, offering possibilities in design.
In contrast, knitting uses a single strand of yarn looped together to form a flexible fabric with interlocking loops. Knitting techniques can create intricate stitch patterns and different fabric structures.
The choice between weaving and knitting depends on the desired properties of the fabric. They include drape, stretch, and strength, influencing the final appearance and functionality of the textile product.
Finishing and treatments
After the fabric is ready, it goes through finishing processes to make it look better and improve its properties.
Initially, fabrics may undergo scouring to eliminate any remaining impurities, followed by bleaching procedures to achieve a desired white color.
Then, fabrics undergo dyeing, offering a wide array of color options using pigments or dyes. Also, treatments like wrinkle resistance and waterproofing can enhance the fabric’s performance for specific requirements.
These finishing processes play a crucial role in determining the final look, feel, and functionality of the fabric. They ensure it meets the intended aesthetic and practical requirements before reaching the market.
Learn more: Discover the best types of fabric for sublimation printing
How to identify the characteristics of fabric fibers?
From the simplest to the most complex, there are several ways to identify the characteristics of fabrics:
- Label Information: fabric rolls usually come with an identification label at the end. This label contains important information, such as the composition.
- Appearance: observe the color and shine of the fibers, which can indicate the type of material. In general, synthetic fabrics tend to be shinier than natural ones.
- Feel: touch the fabric to assess its softness. Natural fibers like silk and cotton tend to have a smoother feel. Synthetic fibers like polyester may feel slicker.
- Burn test: burn a small tip of the fabric and pay attention to how it behaves and to the smell. Synthetic fibers have a smell like burning plastic. Meanwhile, natural fibers may have a smell more like burning hair.
- Microscopic examination: there are online options for small tools specifically for fabrics. They enlarge the image of the fabric on your cell phone screen, and you can closely observe the fibers. This requires some knowledge of textiles.
- Specialized labs: If other options don’t work, and you need a detailed examination, find a specialized lab. Professionals will be able to deliver a complete report to you.
How can fabric creation impact your fashion manufacturing?
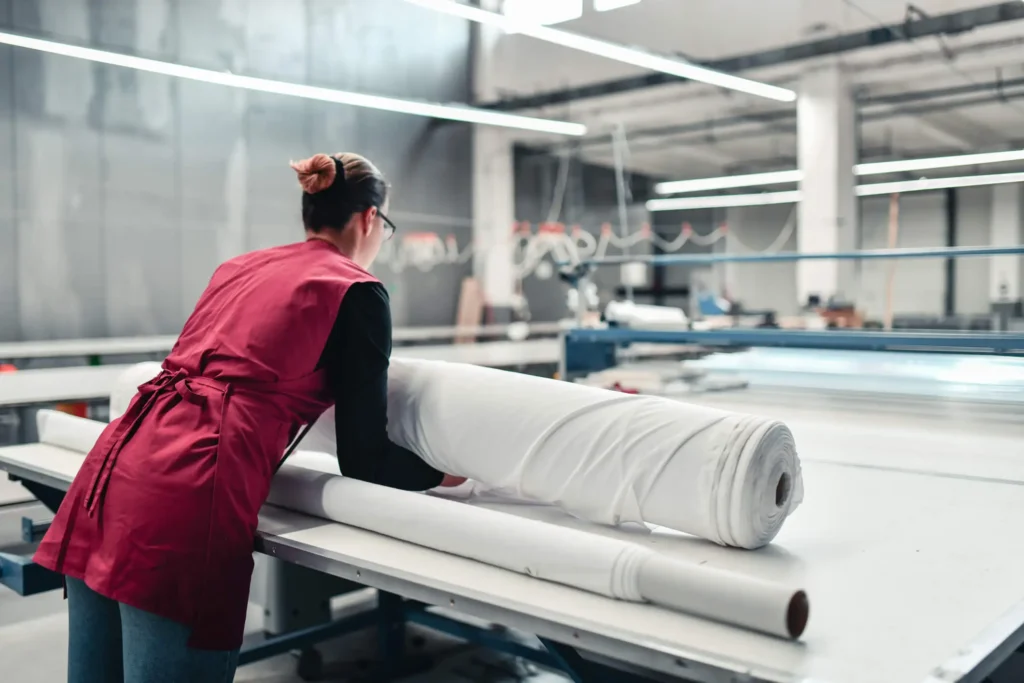
Fabric creation influences not only the aesthetics and functionality of garments but also broader aspects such as product distinction, customer perception, and sustainable practices.
By carefully selecting and utilizing fabrics, fashion manufacturers can create products that resonate with consumers, uphold ethical practices, and minimize their environmental impact.
Product distinction in the market
Investing in innovative and unique fabrics can set your brand apart from competitors. It fosters the creation of a distinct identity and attracts a specific customer base.
The benefit of custom fabric creation for fashion designers is enhanced uniqueness.
Stella McCartney is probably the most famous example of a designer who made a fabric her trademark. The English brand is famous for using sustainable practices in fashion. They use Mylo, a leather alternative made from mushrooms.
On the other hand, the Brazilian brand Farm is world-famous for its colorful and creative prints, all made in-house.
These methods of fabric creation help prevent imitation and establish your brand’s recognition for its unique aspects.
Learn more: Meet 8 iconic fashion designers of the moment to inspire you
Perception of quality and value by customers
Using high-quality fabrics can elevate the perceived value of your garments. It enables you to charge higher prices and attract picky customers.
Fabric creation from sketch allows for the development of exceptional properties, such as appearance, durability, or wrinkle resistance.
These kinds of benefits can enhance customer satisfaction and reinforce perceptions of quality.
Learn more: How to obtain quality and precision in the cutting fabric process?
Impact on sustainable and social issues
Fabric creation plays a critical role in addressing the ecological footprint of the fashion industry.
Sourcing and using eco-friendly fabrics like organic cotton, recycled polyester, and made from biological materials can demonstrate your commitment to environmentally conscious consumers.
Ensuring ethical practices throughout the fabric supply chain is also an aspect to keep an eye on. From raw material production to manufacturing, careful selection builds brand reputation.
Fair profit models that benefit everyone involved in product manufacturing and social issues are becoming more popular.
Take the example of Ninety Percent, from London. 80% of its profits go to charitable causes, and 10% to people who make their collections.
How can technology assist in fabric creation?
Technology can be a powerful ally in fabric creation. Specialized software programs assist in designing prints, allowing designers to test patterns and colors directly on their computer screens.
Creating on 3D mannequins offers another significant advantage. It empowers designers to apply their created prints and visualize how they look on prototypes. Additionally, 3D designs allow for the simulation of the drape and texture of fabrics.
This approach significantly streamlines the fabric creation process, as physical production starts only after digital approval, minimizing costs and material waste.
Create your collection with the best fabrics and cutting-edge technology
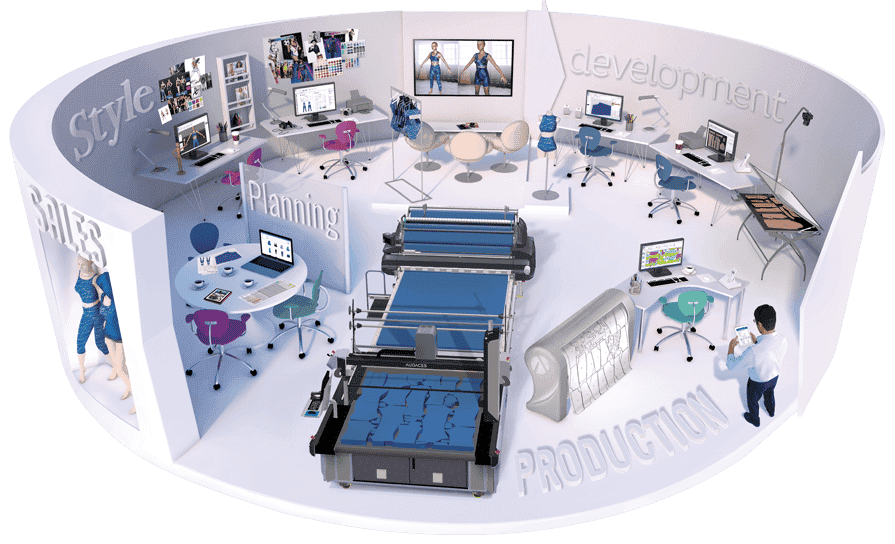
Audaces360
Audaces360 stands as the most comprehensive software solution to optimize your entire creation, development, and production process.
It functions seamlessly from start to finish, connecting your team and simplifying workflow.
These are some of the key benefits:
- Design garments with precision using 2D vector tools, generating automated spec sheets and pre-costs.
- Visualize and refine your designs on a virtual mannequin.
- Leverage AI technology to enhance your design process.
- Manage your collection end-to-end from the palm of your hand.
- Create accurate and efficient digital patterns for production.
- Optimize fabric usage and minimize waste with automated marking.
Explore the insights of our comprehensive guide to fabric types. Download our e-book for free!
FAQ
Fabric creation serves as the base upon which fashion designers build their creations. The properties and textures of fabrics define design choices, influencing fit, draping, and overall style.
As you might imagine, fabric creation involves numerous steps. Different suppliers carry out each of these stages, requiring several skills and machinery.
Fiber selection, spinning, weaving and knitting, and finishing and treatments.