Summary
- To stand out in the fashion and textile industries, prioritizing innovation and high quality is essential.
- Ensuring precision in the fabric cutting process is the starting point for guaranteeing a flawless product for the customer.
- Use technology to your advantage to optimize your production. Try Audaces360 multisolution for free today!
Cutting fabric to make excellent quality products for those involved means directly offering the best to your customers while optimizing the entire value chain.
Today, even more than the quantity and speed of production, the precision in cutting fabrics counts, but above all the availability and flexibility in managing different materials and productions.
For a company operating in the textile world, therefore, quickly adapting and meeting market needs is essential to achieving business objectives.
If you want to know how quality and precision materialize inside a textile confection, read this article that we have prepared especially for you.
Sumário
Cutting fabric: why quality and precision are decisive?
In today’s market, anyone who works in the textile world knows well how the quality and precision of fabric cutting have a decisive impact on customer satisfaction and process optimization, so they are as much a priority as speed and production volumes.
Making a poor quality cut, in fact, in addition to generating customer dissatisfaction, can often lead to the need for rework slows down production processes, as well as increases costs.
In the following paragraphs we will delve into the subject!
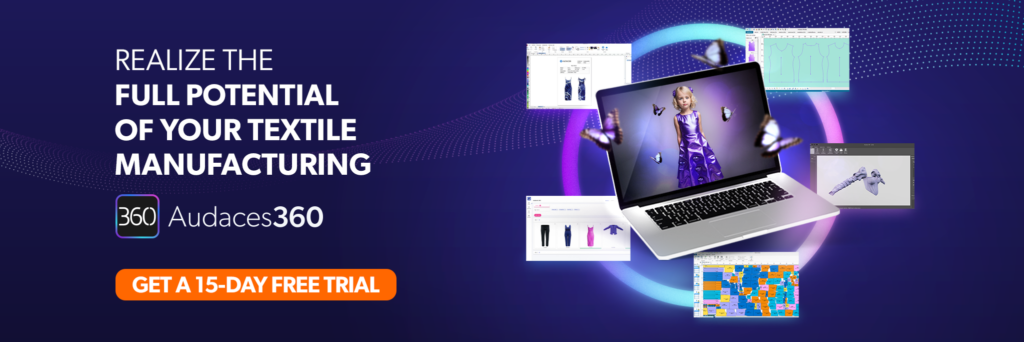
Quality and precision: unity is a strength
The quality of the fabric cut, combined with the precision, allows for optimizing the times of the subsequent sewing, storage, and assembly processes.
If the company that deals with the production of semifinished products provides a product of impeccable quality, the subsequent sewing and packaging operations will not be delayed, and therefore there will be no complaints or disputes about the produced parts.
It is always the precision and quality of the cut that allows for considerably optimized times because finishing operations are no longer necessary.
For example, in the event that it is necessary to cut jeans or other thick materials, the quality of the fabric cut is realized in the reduction of the jagged effect caused by the blade.
In the case of leather cutting, for example, perhaps in the world of leather footwear, it goes without saying that precision must be to the millimeter, to avoid wasting precious material.
The impact of cutting fabric quality on production costs
In addition to the obvious advantage in terms of reduced production times, thanks to the possibility of avoiding the finishing phases, greater precision in cutting allow the safety distance between pieces to be reduced to the maximum, maintaining high quality so as not to incur in products defective and eliminate the possibility of waste.
Nowadays, the evolution of cutting systems allows obtaining a positive ROI from the automation of processes, even in tailoring laboratories that carry out custom processes.
In fact, until a few years ago the comparison between manual and automatic cutting was played out in quantitative terms and therefore only made sense for laboratories that needed to increase cutting capacity, thanks to the innovations of 4.0 new opportunities are opening up in terms of adaptability of productions.
For companies, therefore, there is a greater possibility of obtaining new clients and increasing turnover.
Not only that, even the energy absorption has decreased significantly compared to older machinery, allowing you to pay off the investment of new cutting machines in a short time thanks to decidedly lower electricity bills.
The optimization of production costs is also possible thanks to savings in consumables.
Industry 4.0 technologies at the service of cutting fabric
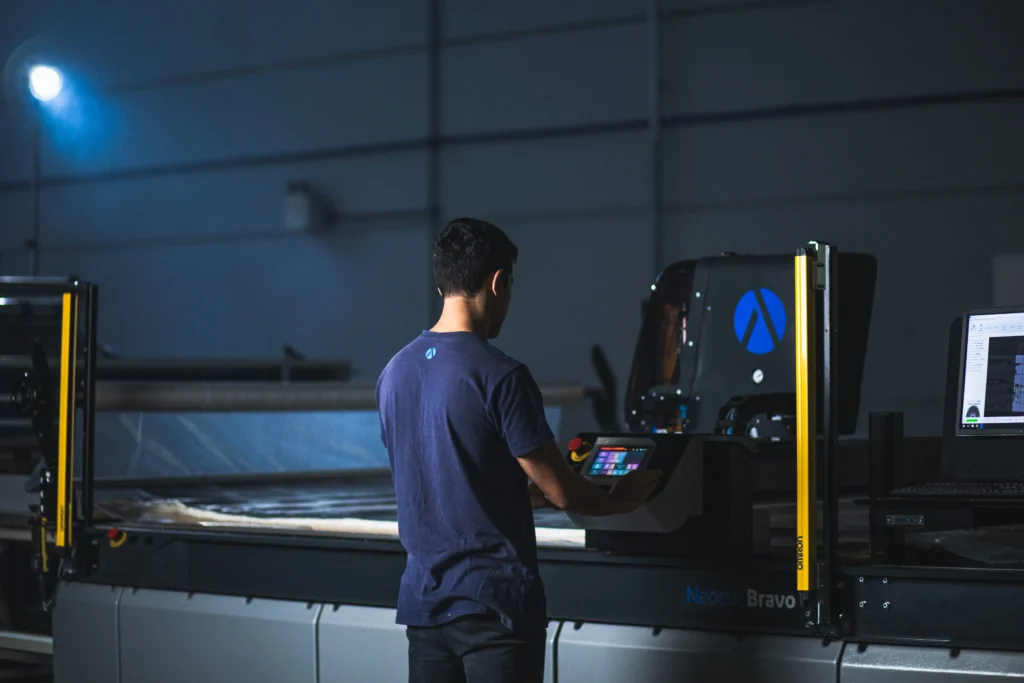
To get a real and tangible benefit from technological innovations, in addition to machinery, it would be desirable to favor a transformation of the entire company to 4.0.
From the point of view of fabric cutting machinery, here is a brief summary of the technologies that aim to optimize production and higher quality of workmanship:
Cloud
The fourth industrial revolution sees in the exchange and aggregation of the so-called Big Data the undisputed protagonists; numbers, analysis, skills, and information are available at hand and in real-time.
Internet of Things
The integration of tools and people is guaranteed by interconnection and allows continuous monitoring of the entire production cycle; information is shared and analyzed in real-time, also avoiding the need for maintenance.
Artificial Intelligence
Machines are not only automated, but are capable of performing operations and making decisions independently.
Smart sensors
The AI applied to sensors and cutters recognizes the material to be cut, analyzes its thickness, calculates the number of cuts and the speed, depending on the stress suffered, and programs the sharpening of the instrument.
Thanks to the transition to Industry 4.0, companies in the textile sector can acquire adaptability and flexibility never seen before, responding promptly to customer needs and market changes, with the advantage of greater efficiency and quality always at the forefront, height of expectations.
Possibility to cut technical fabrics or thick materials
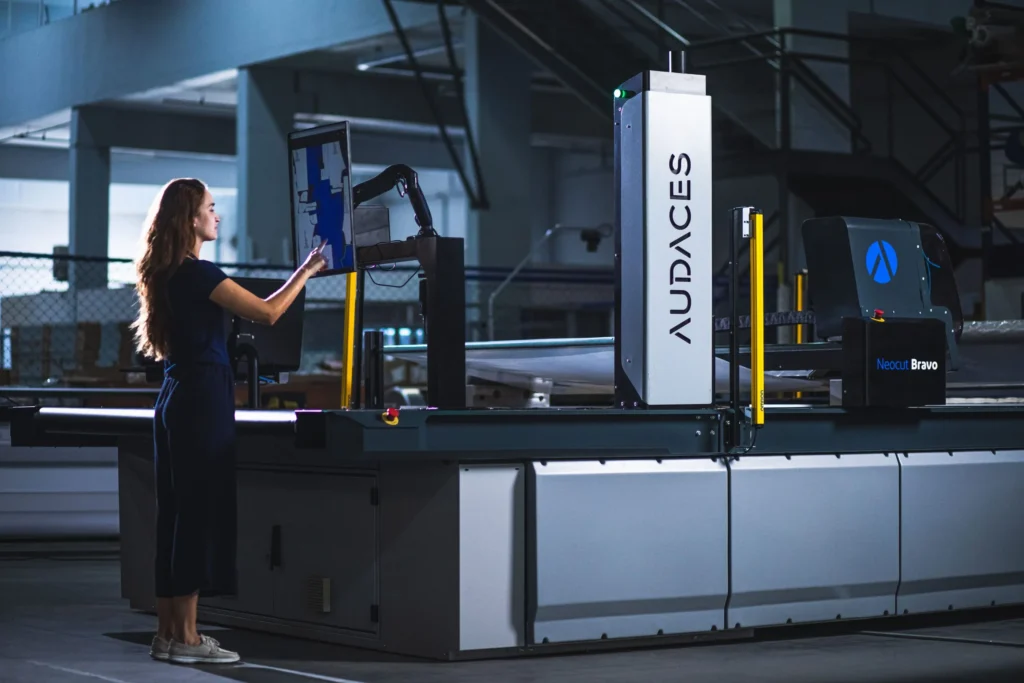
The possibilities offered by innovative machinery are almost limitless. Unlike laser cutting of fabric, in fact, there are no materials whose processing is not recommended or unattainable.
Carbon fibers, glass fibers, synthetic materials such as eco-leather, thick fabrics such as jeans, or extremely delicate fabrics can be cut safely, without risky consequences in terms of harmful emissions, fumes, or flammability.
The blade is monitored to ensure precise and safe cuts, and built-in automation lets you schedule outages for sharpening or replacement.
Reduction and saving of waste
Both in the clothing textile sector and in the industrial world, the cost of raw materials has a considerable weight throughout the production cycle.
The goal of cost optimization becomes achievable, even if high-quality materials or particularly elaborate technical materials are used, thanks to the higher quality and precision of the cut.
Due to the perfection achieved by state-of-the-art machinery, even sharp-cut seams can be performed without difficulty, and waste is reduced to a minimum, avoiding heavy budget impacts.
The technical aspect, combined with the continuous monitoring made available by Industry 4.0, allows for extremely efficient and sustainable production.
Optimization of production start-up times
As we have seen in the previous paragraphs, today’s competition is no longer played so much in the field of the number of processing volumes, as in their variety.
Dividing production batches for different specialized suppliers only extends production times, for this reason having the possibility of adapting your cycles to the different needs of the moment allows you to quickly react and satisfy market demands.
Even the possibility of creating samples, prototypes, and individual parts can be strategic for companies because they demonstrate their competence, as well as the quality and precision of the processes, which can later be replicated in real production.
As we said before, the opportunities that are also created for laboratories that perform manual cutting on behalf of third parties turn out to be decisive for the development of the market, not so much in terms of volumes and cutting capacity, but rather in terms of adaptability to requests, without having to give up a contract because it is too complicated to manage.
Improve customer loyalty with the best of technology
The quality and precision of the cut, as we have seen, affect the optimization of the processes by eliminating the need for further processing.
This advantage is realized in companies that deal with drawing, cutting, and sewing because they have a unique opportunity to save time and costs.
Even companies that deal exclusively with slicing, and then move the processing to an outside lab, can benefit greatly from increased slicing quality and accuracy.
Disputes related to the semi-finished product are the order of the day and a return runs the risk of compromising compliance with delivery deadlines and, as a direct consequence, also the relationship with the client company.
Today more than ever, we know how customer loyalty and retention are strategic to increase the turnover of a company because the costs to acquire new customers are quite high.
Meeting demands, meeting flexible needs, and servicing even the most innovative technical fabrics allow you to pave the way for upselling and cross-selling opportunities.
If you are interested in learning more about fabric cutting and how technologies inspired by Industry 4.0 could help you produce more and better, we invite you to download our e-book:
FAQ
The quality and precision of fabric cutting have a decisive impact on customer satisfaction and process optimization, so they are as much a priority as speed and production volumes.
In addition to the obvious advantage in terms of reduced production times, greater precision in cutting allows the safety distance between pieces to be reduced to the maximum, maintaining high quality.
These advancements can significantly reduce waste, optimize production start-up times, and offer a range of other benefits.