Summary
- Textile equipment maintenance is essential for ensuring smooth production.
- There are different types of maintenance, each impacting your equipment in a unique way.
- Leverage technology to boost your production. Try Audaces360 for free and discover how.
Over time, machines used in the textile industry can develop functional issues and thus require repairs. For example, fabric cutting machine maintenance demands proper equipment and skilled personnel to ensure the work is done correctly.
When performed preventively, equipment maintenance helps reduce costs and avoids production losses.
Learn more about textile equipment maintenance and how it can benefit your fashion business!
Enjoy your reading.
Sumário
Why is keeping up with equipment maintenance so important?

Maintaining your equipment is critical. This ensures that your machines last longer, operate efficiently, and are safe and reliable for operators.
A well-maintained textile equipment can have a longer lifespan, which is why regular maintenance is crucial to ensure both quality and safety in production.
Some benefits of textile equipment maintenance include reduced production costs, fewer unexpected breakdowns, minimized premature wear, and more.
In addition to regular maintenance, it’s essential to thoroughly understand your equipment and its manual and to have access to qualified technical support.
Having a skilled technician who understands the brand of your machines is crucial, along with original parts and accessories being readily available.
Machine operators can assist in equipment maintenance by checking motor components daily before production begins.
When should textile equipment maintenance be done?
The frequency of maintenance depends on machine usage, but how the equipment is used and cared for can reduce the need for repairs.
It’s important to ensure the equipment has all necessary materials, such as oil and gears. Are the filters being changed? How often are cutting tools sharpened or replaced?
Maintenance can be scheduled based on hours of operation or every X number of months, depending on the equipment’s brand. This information is usually provided in the user manual and should be strictly followed.
Also, remember that the more you use the equipment, the more attention it requires.
What types of maintenance can be done on textile equipment?
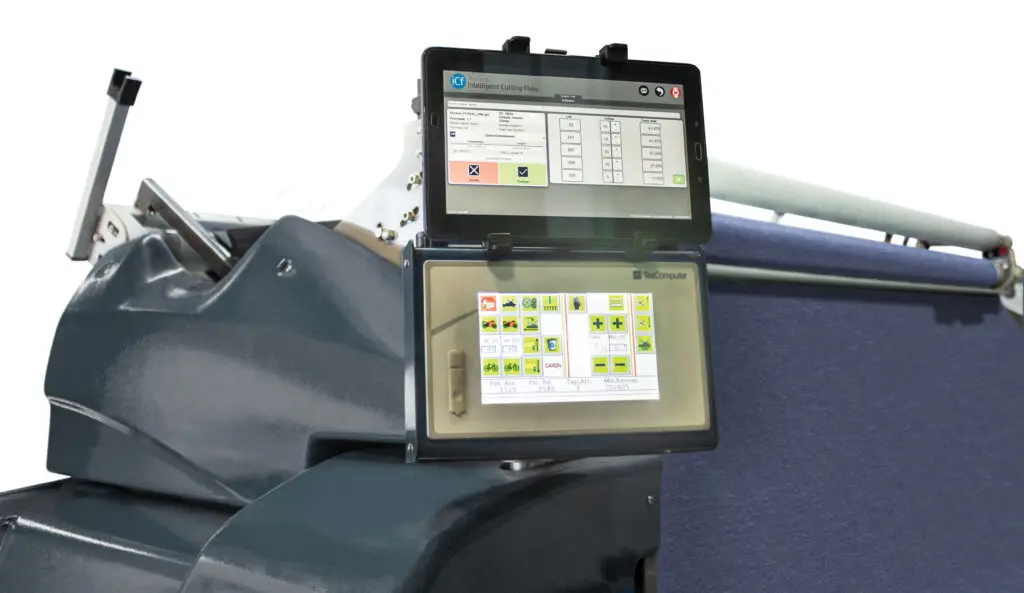
If your textile equipment needs maintenance, there isn’t just one type.
Here are the different kinds of maintenance that equipment like this might need:
Preventive maintenance
Preventive maintenance aims to avoid machine breakdowns or performance drops. It can prevent equipment downtime and even accidents.
This maintenance is pre-scheduled and performed periodically. It involves cleaning the machines, as well as replacing and repairing worn-out parts.
Corrective maintenance
Corrective maintenance is carried out after the machine has already shown signs of malfunction or even failure.
This can be done in two ways: planned, when the company detects that the machine isn’t performing as it should, or unplanned, when the equipment is already broken.
After replacing parts or making any changes to the machine, it’s essential to test the equipment to correct any potential damage and protect the operator.
Predictive maintenance
Predictive maintenance uses software that analyzes machine performance during use, identifying factors that could lead to future issues.
It is highly effective, as it ensures action is taken as soon as a malfunction is detected.
Prescriptive maintenance
When talking about prescriptive maintenance, we’re talking about technology! This maintenance relies on technological resources to analyze precise data about the ongoing activities.
Benefits of this maintenance type include automation, cost savings, precision, capacity optimization, and increased availability.
Detective maintenance
Detective maintenance focuses on protecting the equipment.
By diagnosing early-stage failures, you can reduce wear and prevent machines and components from stopping or jamming. This also helps avoid workplace accidents.
Total productive maintenance
This approach aims to maximize equipment efficiency. The goal of total productive maintenance is to enhance the machine’s functionality, promoting autonomous improvements.
It also allows for maintenance planning and proper operation of the equipment, ensuring all components are correctly checked.
Who should perform equipment maintenance in a production facility?
Knowing that there are various types of maintenance for textile equipment, it’s important to emphasize that this maintenance must be performed by a qualified professional.
The most suitable person for this task is a mechanic specializing in cutting machines. They possess the necessary knowledge of the system and specific features of this type of equipment.
If your equipment requires repairs, contact a service provider with specialists to ensure both quality and safety for your machinery.
How does Audaces technical support work?
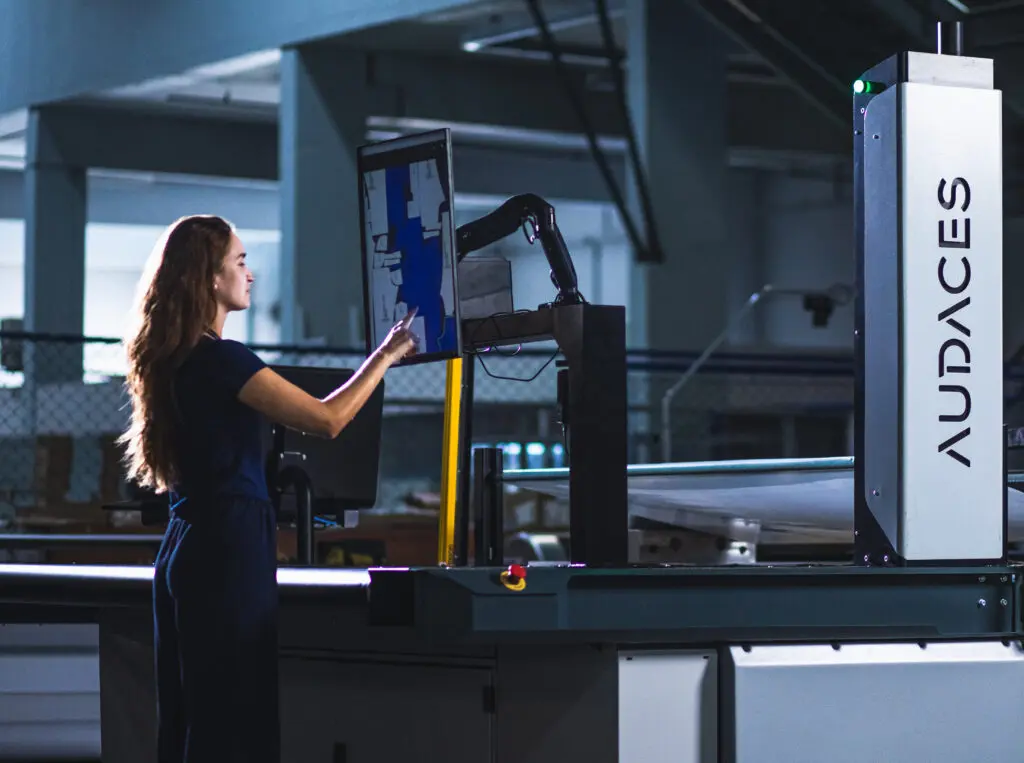
If you use Audaces systems and machines, you’ll be pleased to know we offer exclusive support to assist you!
Audaces is continuously seeking ways to improve customer communication to offer faster and more practical solutions.
In addition to phone support, we also offer chat services. On our website, you can also locate authorized service centers for our machines near you!
To stay updated on changes in our software and learn more about our equipment, you can join our community and access our knowledge base, where you’ll find articles specifically designed to answer your questions.
Did you enjoy learning how to extend the life of your cutting machine? Download for free:
FAQ
Textile equipment maintenance extends its lifespan and ensures the operator’s safety.
According to the dates recommended in the machine’s manual or when the operator notices any type of defect.
There are six types: preventive maintenance, corrective maintenance, predictive maintenance, prescriptive maintenance, detective maintenance, and total productive maintenance.