Summary
- The fashion production process encompasses all the steps involved in clothing manufacturing.
- Without careful planning, it can lead to costly reworks and delays in launch and delivery.
- Simplify your fashion company with technology. Try Audaces360 multi-solution for free!
The planning of the fashion production process impacts a wide range of professionals, including business owners, designers, and pattern makers.
Launching new collections in the market involves a complex series of steps, and everything needs to be perfectly aligned to achieve the best possible outcome.
Different teams work in collaboration, ensuring a smooth handoff from one stage to the next. This meticulous planning guarantees that your energy, time, and resources are invested in the most critical aspects of production, leading to on-time delivery.
We’ve listed the key steps to optimize your fashion production process. Keep reading!
Sumário
Why is it important to understand all the stages of the fashion production process?
Having a comprehensive understanding of the fashion production process, including the roles of all teams, empowers you to excel in your own tasks.
When everyone has a clear view of the bigger picture, they can contribute more effectively to solving problems that may arise.
By understanding each step, you can identify areas where delays or inefficiencies occur. This allows for streamlining operations to improve speed, reduce production costs, and make optimal decisions during critical moments.
You can also recognize potential challenges at any phase of the process, allowing for the implementation of quality control measures. This ensures consistency in quality across all products.
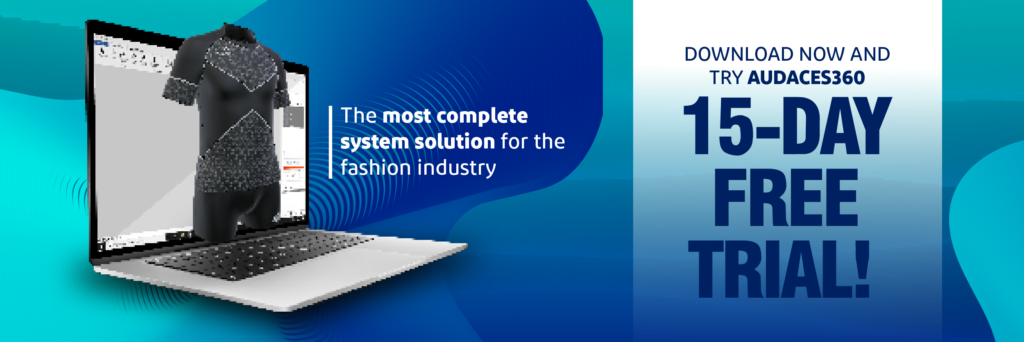
How does the fashion production process work?
The fashion production process is the series of steps involved in developing a fashion product from concept to market.
A well-coordinated end-to-end workflow leads to the creation of competitive products and satisfied customers.
This is how the fashion production process is usually organized:
1) Collection planning
Collection planning is the starting point for everything! This stage guides the entire production journey.
It involves conducting research that is crucial to increase sales for the collection. Investing in this type of research can provide valuable insights to guide your design and marketing decisions.
Here is a list of examples:
- Target audience: identify your ideal customer. Answer the question: who are you designing for? Consider demographics (age, gender, income level), psychographics (interests, values, lifestyle), and shopping habits.
- Competitor analysis: research your competitors. What are they offering? What are their strengths and weaknesses? Analyze their pricing strategies, marketing tactics, and brand image.
- Market trends: identify upcoming trends in fashion, color palettes, fabrics, silhouettes, and popular styles. Use trend forecasting services, fashion publications, runway shows, and street style reports.
- Consumer needs: understand what consumers are looking for in clothing. This may involve comfort, functionality, sustainability, affordability, or ethical production practices. Conduct surveys, and focus groups, or analyze online reviews to gain insights.
Mood boards can be created to visually organize all the gathered information. Designers then conceptualize the collection, defining its essence and aesthetic.
Learn more: 7 steps to develop your fashion collection plan
2) Design and sampling
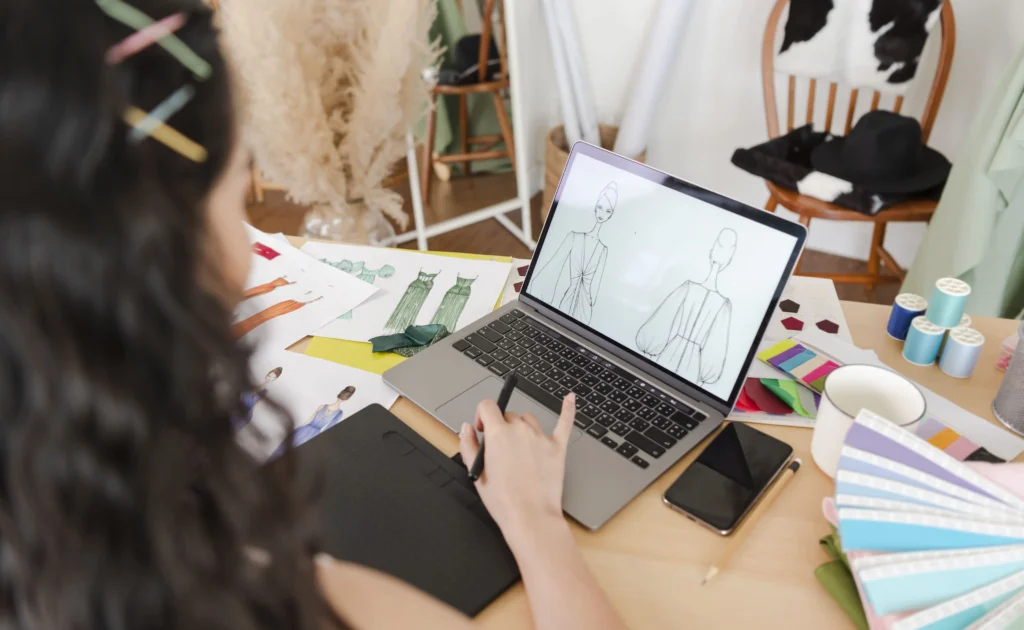
Building upon the established design direction, the references from the previous stage are now transformed into technical drawings that accurately depict the final product, including detailed specifications for its fit on the human body.
While traditionally done on paper, the most optimized and precise way utilizes computer-aided design (CAD) software. Technology even allows for 3D mannequin visualization to effectively simulate the fabric’s texture and movement.
Furthermore, this stage introduces the work of the pattern maker, who plays a crucial role in translating the technical drawing into the first physical version of the garment.
The next step is to calculate the costs of producing each item. This is done by considering mainly the cost of materials and labor. The goal is to achieve a price aligned with the planned strategy.
In some cases, it may be necessary to make substitutions to cut costs. This could involve finding alternative suppliers or using simpler materials. However, any changes must be made carefully to not affect the quality of the product.
The final stage is to create the tech pack. This document includes all the measurements and specifications, serving as a guide for the professionals who will be responsible for manufacturing the garment.
Learn more: Learn all about how to draw the fashion sketch for your collection
3) Pattern making and marking
Following the approval of the sample garment, the pattern maker meticulously refines the pattern, ensuring it embodies the designer’s envisioned fit.
Additionally, the pattern maker is responsible for grading, which is adapting the base pattern to accommodate the different size variations in which the garment will be produced.
Digital tools are extremely helpful in this stage of the process to ensure the accuracy of the measurements, which significantly affect the final product.
With the patterns finalized, the marking process starts. It involves strategically arranging the patterns on the fabric to minimize waste.
There are software programs that can automate this process, calculating the optimal marking to achieve the most efficient fabric utilization. Integrated solutions can even transfer digital patterns directly to marking.
Learn more: Understand the importance of a pattern maker for fashion manufacturing
4) Fabric cutting
Once the fabric has been spread, it is prepared for the cutting stage, which can be performed manually or using automated machinery.
Accuracy is also important here because once the fabric is cut, it is difficult to correct any errors and fabric will be wasted.
The cut pieces are then organized into packages, ensuring all the necessary parts for the complete garment are readily available for the next stage.
Learn more: Why invest in a good fabric cutting table for garment production?
5) Sewing and finishing
Now it is time for the sewers to receive the pre-cut garment components for assembly.
Prior to this stage, there may be some intermediate steps depending on the desired outcome, like the application of localized prints, for example.
Sewing is also an opportunity to add value to the garments. Special seams can be used to create visual and design effects, like decorative topstitching, if this was included in the initial design.
Upon completion of sewing, the garments undergo a rigorous quality inspection to identify any potential defects, guaranteeing that the customer receives a flawless product.
Learn more: How to define production stages using a textile flowchart
How to optimize the fashion production process?
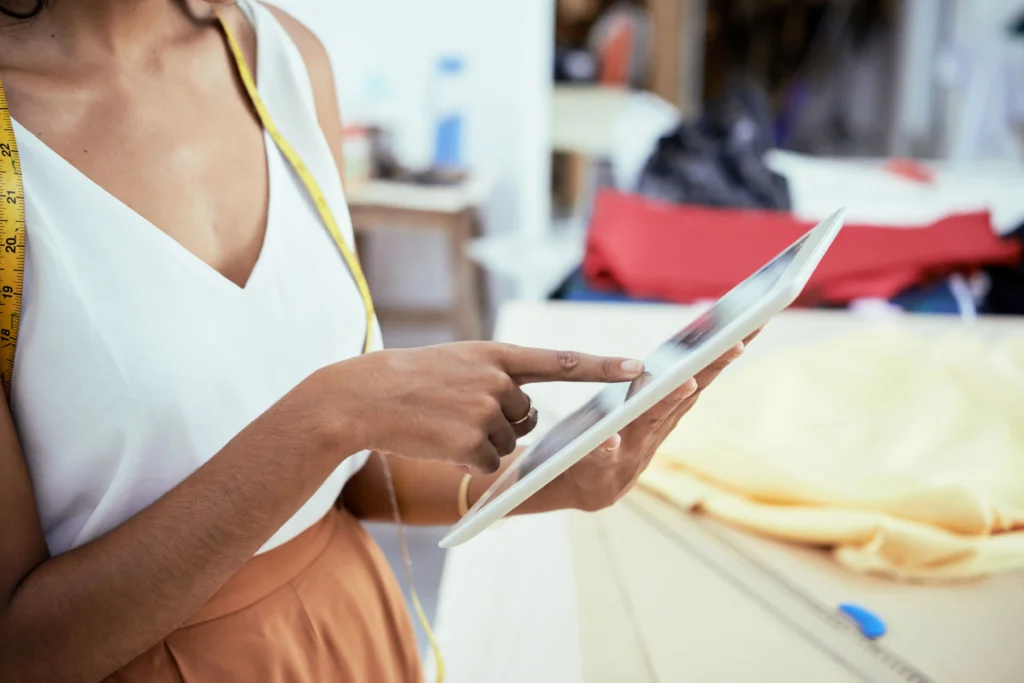
Streamlining the workflow of your company brings several benefits, impacting everything from your collection planning to customer satisfaction.
It can reduce lead time, allowing you to respond quickly to market trends and customer demands, and minimize waste, leading to cost savings and a more sustainable operation.
There is a multitude of ways to optimize efficiency, accuracy, and creativity in your fashion production process.
We prepared a guide with the best ones for you:
Standardizing production steps
Streamlining your workflow by standardizing processes eliminates the time wasted on constantly planning how tasks should be done.
Systematized procedures avoid bottlenecks that can slow down production and ensure everyone on your team is on the same page.
It facilitates seamless handoffs between teams and enables consistent execution of tasks, maintaining the same quality in each batch.
The resulting time savings free up professionals to focus on strategic initiatives that drive productivity and growth for your business.
End-to-end process tracking
Continuously monitoring your fashion production process from the very beginning with real-time tools empowers you to catch errors and delays as soon as they happen.
This proactive approach allows you to swiftly address any issues, preventing reworks, and enables you to find opportunities for improvement and cost reduction.
By analyzing production data, you can detect areas for streamlining processes or optimizing material usage. These improvements can translate to significant savings over time.
It is also a way to ensure the final quality of your collection. By tracking each item throughout the production journey, you can identify and rectify any quality issues before they reach the customer.
Moreover, this level of transparency grants you greater control over your entire production process, allowing for better planning and resource allocation.
Learn more: How can your apparel business integrate PLM and ERP?
Automating operational activities
Automating tasks brings agility to your fashion production process, especially by replacing repetitive tasks such as data entry into spreadsheets.
Manual tasks are time-consuming and always run the risk of errors. Information can also be lost when it needs to be passed from one team to another.
Ideally, solutions for each stage should be integrated and information should be visible to all areas involved.
An example of improved time, reduced waste, and consequently improved revenue is automatic marking solutions. Manual marking is a meticulous task that relies heavily on the professional’s expertise to avoid wasting material.
In contrast, automated tools utilize advanced algorithms to calculate the most efficient marking, significantly reducing fabric waste and boosting profitability.
Learn more: Find out how – and why – to apply textile automation in your company
Incorporating cutting-edge technology
In today’s competitive fashion landscape, technology is no longer a luxury, it’s a necessity. Just like it has revolutionized countless other industries, it is transforming the way clothing is designed, produced, and managed.
Digital tools can lead fashion businesses to various benefits that reduce errors, enhance productivity, improve profitability, and eliminate waste.
Maintaining close oversight of every production step is essential. Modern solutions provide real-time monitoring with mobile versions, empowering you to stay informed and make data-driven decisions from anywhere.
Another advantage is improved safety. Automating some tasks, particularly those involving heavy machinery, can reduce the risk of accidents and injuries.
One of the biggest hurdles to implementing digital solutions can be the fear of complexity. However, modern software is designed with user-friendliness in mind.
The intuitive interfaces and readily available training resources ensure a smooth transition for teams, regardless of their prior technical experience.
By embracing these technological advancements, fashion businesses can gain a significant competitive edge.
From streamlining processes and optimizing production to fostering innovation and safety, technology is paving the way for a more efficient, profitable, and sustainable future for the fashion industry.
Learn more: Explore the benefits of industrial technology in the fashion sector
Boost your fashion production process with Audaces solutions
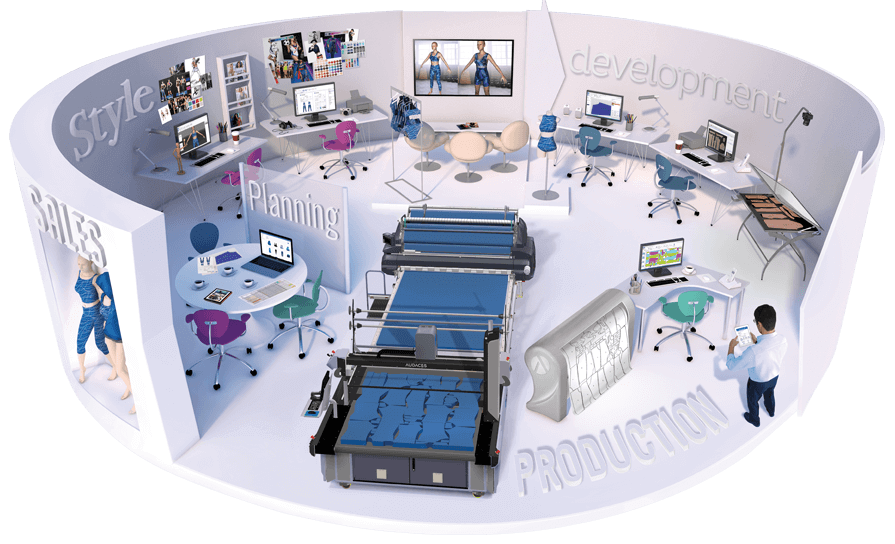
Audaces360 is a comprehensive solution that integrates advanced technologies to optimize production processes in the textile industry, suitable for companies of all sizes and types.
This software was developed to meet the needs of the textile and clothing industry and designed to streamline and speed up the production process.
Audaces360 offers a wide range of functionalities, including digital pattern design and approval, fabric marking and cutting, production management, and integration with other textile machines.
The goal of this solution is to increase efficiency, reduce waste, and promote more agile and competitive production.
These are the tools that integrate this multi-solution:
- Isa: the fashion PLM to plan and manage your collection in real-time.
- Fashion Studio: to design your creations directly in a three-dimensional environment.
- Idea: to automatically create vector drawings, technical sheets, and pre-costs.
- Digiflash: to scan your patterns with a simple photo.
- Pattern: to create patterns and develop sizes directly on the computer.
- 3D: to sew your digital patterns and simulate the fit on a 3D avatar.
- Marker: to increase efficiency with automatic marker creation.
- Supera: to save time and fabric with queue management.
- Sofia: to unlock new possibilities with the help of Artificial Intelligence.
Find out how Audaces360 drives digital transformation with our free e-book!
FAQ
Having a comprehensive understanding of the fashion production process, including the roles of all teams, empowers you to excel in your own tasks.
Collection planning, design and sampling, pattern making and marking, fabric cutting, and sewing and finishing.
Standardizing production steps, end-to-end process tracking, automating operational activities, and incorporating cutting-edge technology.