Summary
- Printing on fabric is a method for applying designs, patterns, or images to fabrics.
- Over time, printing on fabric has evolved into a highly technological process.
- Create your collection with Audaces online and practical. Try Audaces360 multisolution for free now!
In the apparel sector, many resources are being developed to add value to products and brands, and printing on fabric is one of them.
There are several types of printing on fabric, and the designer must choose the one that best suits the company’s universe.
Some printing methods include screen printing, by cylinder or frame, digital or manual, as well as other techniques such as devoré, flocking, transfer, and tie-dye.
Clothing brands increasingly invest in these resources, as they can give their products a competitive edge. Understand better how this process works and how to apply it to your company.
Sumário
Enjoy your reading!
How relevant is printing on fabric in the fashion industry?
Printing on fabric plays a crucial role in the fashion industry, being a method for applying designs, patterns, or images to fabrics.
Textile printing offers a wide range of design options, allowing clothing manufacturers to create a variety of unique styles, patterns, and colours. This enables product customization according to consumer preferences.
Furthermore, fabric printing is an effective method to keep up with fashion trends, as prints can be changed and updated to mirror shifts in consumer tastes and cultural influences.
It enables the creative expression of designers, fostering innovation in the fashion industry. New methods, color combinations, and unique designs can be developed to differentiate brands and create distinctive identities.
Prints often play a significant role in visually attracting consumers, evoking emotions, telling stories, and establishing an emotional connection between the product and the consumer.
Well-executed printing can add value to textile products, allowing brands to justify higher prices. Exclusive and high-quality prints are perceived as luxurious and desirable by consumers.
In a competitive market, printing can be a powerful tool to differentiate a brand. It allows brands to create a unique visual identity that is recognizable and memorable.
Prints can be applied to a wide variety of textile products, including clothing, accessories, decorative fabrics, and footwear, among others, expanding the reach of printing in the fashion industry.
Discover the evolution of printing on fabric methods
Methods of printing on fabric have undergone significant evolution over time, driven by technological advances, changes in market demand, and the constant pursuit of more efficient and innovative processes.
Let’s highlight some of these evolutions:
Manual and artisanal printing
In the early days, printing was done manually, often using stamps or carved wooden blocks to apply ink directly to the fabric.
Heat printing
Methods such as heat transfer and sublimation gained popularity. Sublimation, for example, allows the direct transfer of ink from a solid to a gaseous state, resulting in durable and vibrant prints.
Digital printing
The introduction of digital printing revolutionized the industry, allowing high-resolution printing directly onto fabric without the need for screens, providing design flexibility and production speed.
3D printing
3D printing employs advanced technologies to create three-dimensional effects on fabrics, adding texture and depth to prints.
Learn more: Learn what 3D modeling is and its benefits for clothing design and production
Integration of software
The use of advanced software for design, pattern management, and process automation has enhanced accuracy, reduced errors, and streamlined production.
Automation and robotics
Automation is increasingly being implemented in printing, from fabric preparation to print application, improving efficiency and consistency.
Learn more: Find out how futuristic fashion is revolutionizing the industry with technology
Main trends for printing on fabric
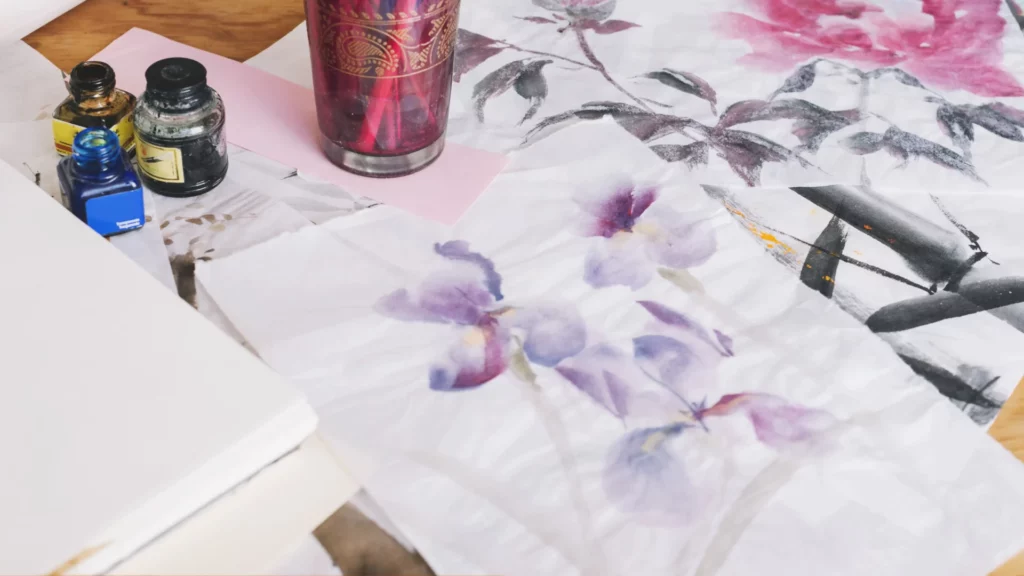
Evolutions and trends reflect the constant pursuit of innovation, sustainability, and creative expression in the printing industry, influenced by social, technological, and aesthetic changes over time. Explore the main trends:
Digital prints
Digital printing is a dominant trend, allowing complex and customized designs with an extensive array of colors and details. It responds to the demand for customization and fast production.
Learn more: Explore the role and benefits of a virtual fashion designer
Botanical prints
Botanical prints are booming, reflecting a desire to reconnect with nature. It incorporates elements such as flowers, leaves and flora-inspired patterns, bringing freshness and authenticity.
Minimalism and geometric prints
Minimalism and geometric prints are in demand, representing a simplistic and elegant aesthetic. Clean lines, geometric shapes, and neutral colours are valued, giving a sense of order and modernity.
What are the most used printing on fabric methods?
There are several ways to apply printing, each offering unique advantages for your work.
Some methods have a long history, being used for centuries, while others emerged with advances since the Industrial Revolution. Get to know some of them:
Screen printing
Screen printing is a traditional and widely used method that involves passing ink through a screen to create precise and durable patterns on a variety of fabrics. It is a versatile and effective technique.
Highly manual, it has evolved over time. Nowadays, although it can still be carried out manually, machines are available to assist in the process.
In this method, ink is pressed and pulled by a squeegee or puller through a polyester or nylon screen. The screen has cutouts through which the ink passes in the desired locations.
The screen has dark and light areas. Dark areas correspond to where the screen was opened, allowing the paint to pass through. Light areas are waterproof, blocking the passage of light. Additionally, during this process, the use of boards to stretch the fabric is essential.
Screen printing offers the possibility to reproduce even photographs. Furthermore, the color system used in printing is CMYK.
Sublimation
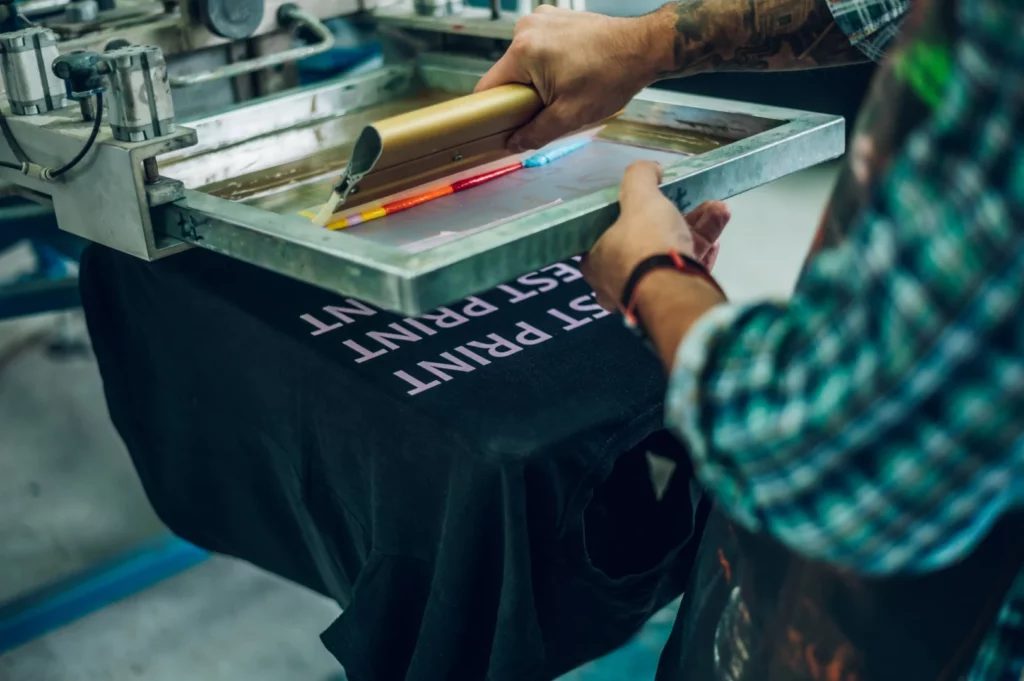
Sublimation is a modern technique that involves printing special inks on paper and transferring these inks to the fabric through heat.
At an affordable cost and providing a high-quality finish, sublimation stands out as one of the main, if not the main, methods used in printing.
Sublimation is a chemical process that transforms the print directly from a solid to a gaseous state, without going through the liquid phase.
This way, the ink, initially in a solid state on paper, converts into vapour when transferred to the fabric, adhering to it.
Although it may seem complex, sublimation application requires only a design on sublimation paper, a press, and a flat surface.
It is important to remember that this process is fast and viable on a large scale, but is suitable for fabrics with a higher percentage of polyester and light colours. Dark fabrics are not ideal for this technique.
Laser printing
Laser printing represents a modern approach that ensures high-quality prints. However, it has some limitations, making it a more limited method. An example is the restriction of fabrics, as the laser can damage the piece.
In this process, a printer that uses conventional toner and transfer paper is used.
Digital printing
Digital printing, a highly technological and innovative technique, stands out as one of the most modern options in printing.
This method employs specific technology that contributes to its higher cost and also imposes limitations on the variety of fabrics due to ink adhesion.
Production involves direct printing of the design onto the fabric surface, with advantages such as the ability to reproduce rich details, precision, and flexibility to experiment with colours, resulting in prints that closely resemble the conceived design.
Learn more: Discover 6 key textile printing techniques and their applications
Discover Audaces solutions for printing on fabric
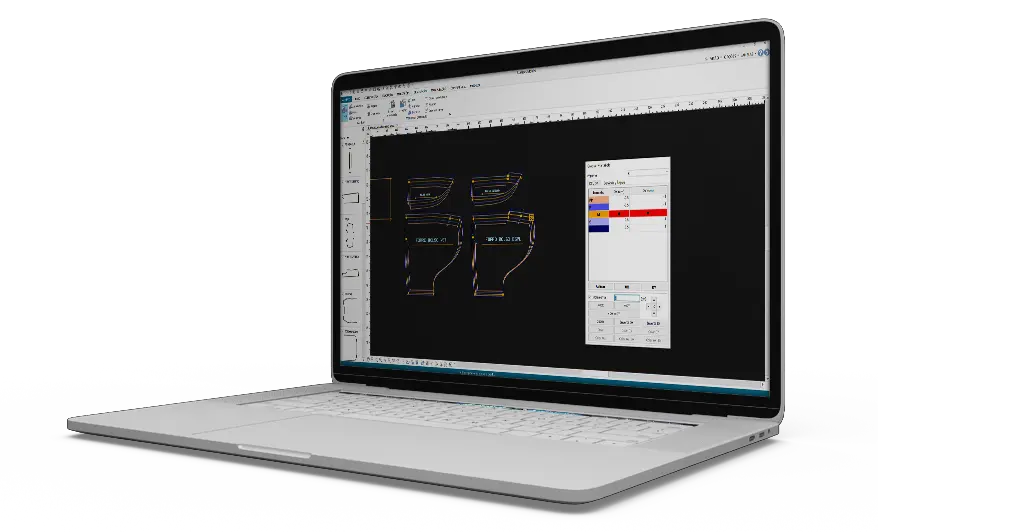
If you aim to optimize your printing process, Audaces Pattern is the ideal solution.
By adopting a computerized method for digital printing, the design is transferred to the fabric without the need for frames or cylinders, using a textile program connected to an industrial printer.
Integrated with the versatile Audaces360 platform, Audaces Pattern is an effective system for working specifically with digital printing. It facilitates the creation of patterns, for localized or all-over prints, making the entire process agile and efficient.
This technology represents a quick, effective, and profitable approach. It allows for the efficient management of prints and patterns, promoting notable agility and time optimization in the production cycle.
Using the right printing on fabric for your company helps you save resources! If you want to learn other ways to achieve this goal, check out our e-book and download it now:
FAQ
Printing on fabric offers a wide range of design options, allowing clothing manufacturers to create a variety of unique styles, patterns, and colours.
Manual and artisanal printing, heat printing, digital printing, 3D printing, software integration, automation, and robotics.
Digital prints, botanical prints, minimalist and geometric prints.