Resumen:
- El lean manufacturing es una forma de gestión que busca reducir los desperdicios en el proceso de producción;
- Aplicado a las confecciones, aumenta la eficiencia, reduce costos y agrega valor a los productos o servicios;
- Para optimizar tu producción de principio a fin, cuenta con la ayuda de la tecnología. ¡Prueba Audaces360 gratis!
En busca de la mejora continua del proceso productivo, muchas empresas e industrias adoptan metodologías de gestión para perfeccionar sus procesos constantemente.
Entre las opciones disponibles, el lean manufacturing es una filosofía que tiene como objetivo el crecimiento y la organización basándose en un principio muy conocido: solo lo esencial es suficiente.
¿Quieres saber más sobre los conceptos del lean manufacturing y cómo funcionan en la práctica? Consulta la guía completa que preparamos.
¡Buena lectura!
Sumário
¿Qué es el sistema lean manufacturing?
El lean manufacturing, o manufactura esbelta, es una filosofía y un sistema de gestión que busca aumentar la eficiencia productiva eliminando los cuellos de botella en la producción.
Esto significa evaluar qué procesos están funcionando de manera eficiente, es decir, utilizando la cantidad justa de recursos (personas, insumos, tiempo), y cuáles están consumiendo más de lo necesario.
¿Cuáles son los 5 principios del lean manufacturing?
Al ser una metodología antigua (pero no obsoleta) y consolidada, el lean manufacturing se basa en 5 principios fundamentales:
1) Identificación de valor
Es la característica que responde a las necesidades del cliente, es decir, lo que considera importante y que satisface sus requerimientos en un tiempo determinado.
2) Flujo de valor
Incluye todo el flujo productivo y los procesos que llevan el producto deseado al cliente. Más adelante entenderás por qué este es uno de los principales aspectos a analizar y “optimizar”.
3) Flujo continuo
Incluye todo el flujo productivo y los procesos que llevan el producto deseado al cliente. Más adelante entenderás por qué este es uno de los principales aspectos a analizar y “optimizar”.
4) Producción jalada
Se refiere a un producto que solo se fabrica en función de la necesidad real o interés del cliente, evitando producir algo que no sea requerido.
5) Perfección
Heredado de su origen japonés, este principio se centra en entregar al cliente el valor correcto a través de un proceso sin desperdicios.
¿Cómo aplicar el lean manufacturing en tu confección?
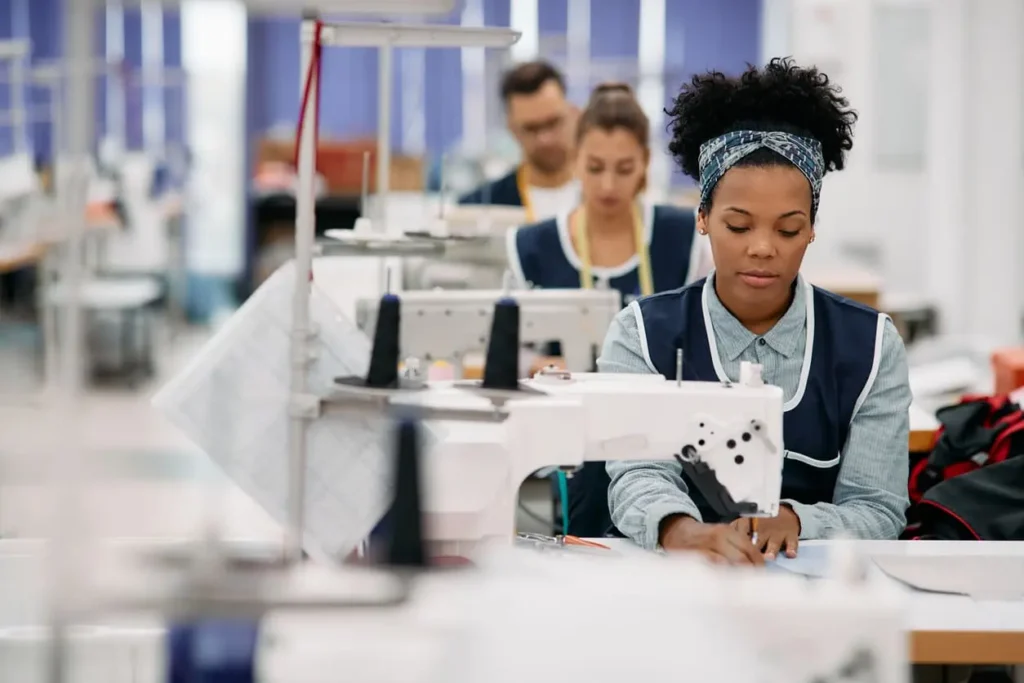
En la práctica, el lean manufacturing tiene una estructura similar a otros sistemas de gestión: debes ir al lugar donde ocurre el problema, evaluarlo, estructurar soluciones efectivas, prácticas y simples, aplicarlas y monitorearlas.
Este es el paso a paso para lograr una producción eficiente en tu confección:
Gestiona bien el inventario
Reducir los inventarios es clave en el lean manufacturing. Una mejor gestión de inventarios reduce costos, ya que menos dinero queda inmovilizado en productos terminados y materias primas.
Además, mejora la calidad porque disminuyen las probabilidades de que los productos se vuelvan obsoletos o presenten defectos en almacenamiento.
Lee más: 7 consejos para controlar el inventario de manufactura de tu confección
Monitorea y controla la calidad
Implementa un sistema de control de calidad definiendo estándares, realizando inspecciones y tomando medidas correctivas cuando sea necesario.
También utiliza herramientas estadísticas para monitorear procesos e identificar posibles desviaciones.
Capacita e involucra a tus empleados
Los colaboradores son el mayor valor de cualquier empresa. Para que el lean manufacturing funcione bien, es crucial que estén capacitados y comprometidos.
Ofrece capacitaciones para que aprendan a identificar y eliminar desperdicios, y fomenta un entorno colaborativo donde todos participen en decisiones y busquen mejoras continuas.
Diseña el layout y la organización de la producción
Un diseño eficiente mejora el flujo de materiales y personas, reduciendo el tiempo de producción y los movimientos innecesarios.
Analiza el flujo de producción para identificar cuellos de botella y actividades que no agregan valor. Organiza el espacio de trabajo manteniéndolo limpio, ordenado y accesible.
Reduce los tiempos de configuración (setup)
El tiempo de setup es el necesario para preparar una máquina para producir un nuevo artículo. Reducirlo aumenta la flexibilidad y la productividad.
Estandariza los procesos de configuración con instrucciones detalladas para cada ajuste, utiliza herramientas que agilicen este tiempo, y motiva a los operadores a proponer mejoras.
Lee más: 4 pasos para que tu proceso de producción de ropa sea perfecto
8 herramientas del lean manufacturing más utilizadas
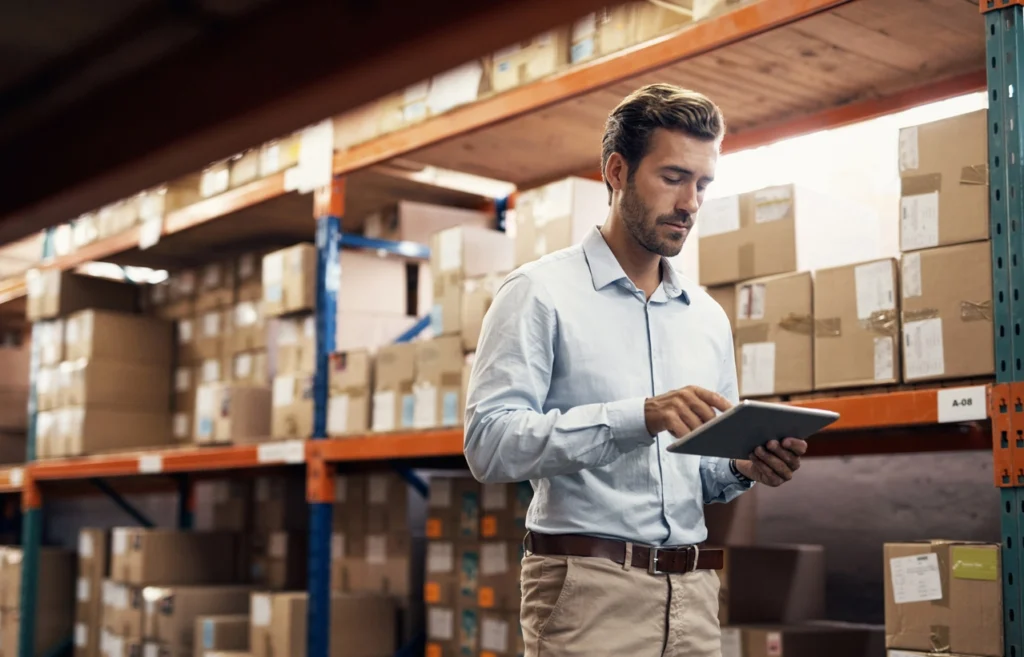
Conoce las principales herramientas del lean manufacturing para mejorar cualquier cadena productiva en el sector textil:
1) Mapeo de la cadena de valor
El mapeo es una herramienta visual que permite visualizar todo el flujo de valor de un producto, desde la materia prima hasta el cliente final.
A través de él, es posible identificar desperdicios y cuellos de botella en el proceso productivo, permitiendo tomar decisiones más acertadas para optimizar el flujo.
2) Just in time
El just in time es una filosofía de producción que busca producir únicamente la cantidad necesaria de productos, en el momento exacto en que son demandados.
En la industria textil, ayuda a reducir inventarios, disminuir el tiempo de ciclo y aumentar la flexibilidad para atender las demandas del mercado.
Lee más: Descubre cómo entregar tus colecciones de moda justo a tiempo
3) Diagrama de flujo textil
El diagrama de flujo textil es una representación gráfica de las etapas del proceso productivo, desde el hilado hasta la confección final.
Esta herramienta permite visualizar la secuencia de las operaciones, identificar los puntos críticos y proponer mejoras en el flujo.
Lee más: 5 pasos para armar tu propio cronograma de moda
4) Takt time
Representa el tiempo disponible para producir una unidad de producto con el fin de satisfacer la demanda del cliente. En otras palabras, es el ritmo necesario para que la producción siga la demanda.
Para calcular el takt time, se divide el tiempo disponible para la producción entre el número de unidades necesarias.
Por ejemplo, si tienes 8 horas de producción al día y necesitas producir 80 unidades al día, el takt time sería de 6 minutos (8 horas x 60 minutos / 80 unidades).
Al calcular el takt time, la industria textil puede ajustar su producción para satisfacer la demanda del mercado y evitar la sobreproducción o la falta de productos.
5) PCP
El PCP (Planificación y Control de la Producción) es fundamental para garantizar que la fabricación de productos textiles ocurra de manera eficiente y dentro de los plazos establecidos.
Generalmente, se realiza a partir de programas especializados con módulos correspondientes a las diferentes etapas de producción.
El PCP optimiza el uso de recursos, reduce los plazos de entrega y mejora el desempeño general de una confección.
Lee más: ¿Qué es el PLM y cómo beneficia tu confección de moda?
6) Metodologia PDCA
La metodología PDCA (Plan, Do, Check, Act) es un enfoque de gestión y mejora continua que ayuda a garantizar que los procesos y proyectos se gestionen de manera eficaz.
Se utiliza para implementar y revisar cambios y mejoras de forma sistemática, y puede resumirse de la siguiente manera:
- Plan (Planificar): identifica problemas o áreas de mejora;
- Do (Ejecutar): pon en práctica el plan;
- Check (Verificar): evalúa los resultados obtenidos;
- Act (Actuar): toma las acciones correctivas necesarias.
7) Mantenimiento preventivo
El mantenimiento preventivo sirve para evitar que los equipos fallen, reduciendo así el tiempo de inactividad y los costos de mantenimiento correctivo.
En la industria textil, el mantenimiento preventivo es esencial para garantizar la continuidad de la producción y la calidad de los productos.
8) Métricas de desempeño (KPIs)
Los KPIs (Indicadores Clave de Desempeño) se utilizan para monitorear el progreso en relación con los objetivos establecidos, identificar áreas de mejora y tomar decisiones informadas.
Estos son algunos ejemplos comunes utilizados en confecciones:
- Volumen de producción: cantidad total de productos fabricados;
- Eficiencia de producción: cantidad de productos producidos en relación con el tiempo y los recursos utilizados;
- Costo por unidad producida: costo total de producción dividido entre el número de unidades producidas;
- Tasa de devolución: porcentaje de productos devueltos en relación con la cantidad de productos entregados.
Lee más: 4 beneficios de la tecnología en la producción de moda
Ejemplos del uso de lean manufacturing en la moda
Para atender a los rápidos cambios del mercado, la industria de la moda necesita ser ágil. El lean manufacturing es un aliado para empresas de todos los tamaños, desde las más pequeñas hasta las grandes minoristas mundiales.
Entre las marcas que aplican el método para mantenerse competitivas en el mercado, están:
- H&M;
- Nike;
- Patagonia;
- Tommy Hilfiger;
- Zara.
Benefícios do lean manufacturing para empresas de moda
El lean manufacturing ofrece una serie de beneficios significativos para las confecciones textiles, entre los cuales se destacan:
Aumento de la eficiencia
La optimización de los procesos y la eliminación de actividades que no agregan valor al producto final permiten que las piezas sean producidas y entregadas más rápidamente.
Lee más: 7 pilares de la industria de la moda para la gestión de la confección
Reducción de costos
Al eliminar desperdicios y mejorar la gestión de inventarios, las marcas pueden minimizar gastos innecesarios en materiales y recursos.
Además, la reducción de tiempos de ciclo y la mejora en la eficiencia operativa contribuyen a disminuir los costos de producción.
Mejora de la calidad
La implementación de sistemas de control de calidad y la búsqueda de la perfección en todos los procesos llevan a una reducción significativa de defectos.
Los productos de alta calidad aumentan la satisfacción del cliente y, como consecuencia, fortalecen la imagen de la empresa en el mercado.
Mayor flexibilidad
Una mayor flexibilidad en las confecciones de moda permite realizar cambios rápidos para atender las tendencias del mercado y las nuevas demandas de los consumidores.
Con procesos más ágiles y eficientes, las marcas pueden ajustar sus líneas de producción, alterar diseños e introducir nuevos productos en poco tiempo.
Satisfacción del cliente
La suma de todos los beneficios solo puede tener un resultado: el aumento de la satisfacción del cliente.
La entrega rápida de productos de calidad dentro del plazo establecido proporciona una experiencia excepcional al cliente y consolida la reputación de la marca.
Haz tu confección más productiva con soluciones Audaces
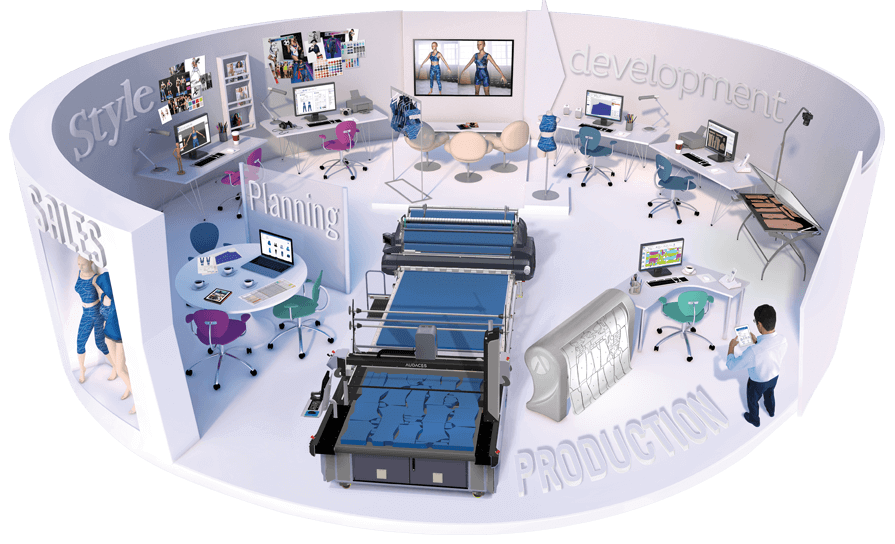
Audaces360
Audaces360 es la solución más completa de tecnología para la industria de la moda. Con esta herramienta, ayudamos a optimizar procesos, eliminar costos innecesarios y explorar todo el potencial de tu producción de moda.
Nuestra plataforma innovadora integra las etapas de creación, desarrollo y producción para agilizar tu flujo de trabajo.
Sala de Corte Audaces
Al adoptar tecnología de punta, las confecciones pueden lograr mejoras significativas en sus procesos, desde la agilidad en el diseño hasta el aumento de la eficiencia productiva y la reducción de costos. Para hacer realidad todo esto, creamos la Sala de Corte Audaces.
Nuestro equipo de especialistas evalúa cuidadosamente las necesidades de tu empresa y crea un informe completo.
Luego, desarrollan un proyecto personalizado para que tu empresa pueda alcanzar los objetivos y maximizar su potencial productivo.
Confía en lo mejor de la tecnología para automatizar tu producción. Con la Sala de Corte Audaces, es posible realizar cortes impecables con curvas y detalles complejos, acelerando tus entregas y minimizando el desperdicio de tela.
Preguntas Frecuentes
Lean manufacturing, o manufactura esbelta, es una filosofía y un sistema de gestión que busca aumentar la eficiencia productiva mediante la eliminación de cuellos de botella en la producción.
Identificación de valor, flujo de valor, flujo continuo, producción jalonada y perfección
Mantén una buena gestión de inventarios, supervisa y controla la calidad, capacita y compromete a tus empleados, diseña el layout y trabaja en la reducción de tiempos de configuración (setup).